Why Cast Gray Iron Is Preferred for Its Wear Resistance?
Cast gray iron has long been a preferred material in various industries due to its exceptional wear resistance properties. This versatile metal alloy, known for its characteristic gray color resulting from graphite flakes embedded within its microstructure, offers a unique combination of strength, durability, and cost-effectiveness. In this blog post, we'll explore the reasons behind cast gray iron's popularity for applications requiring high wear resistance and delve into its properties, manufacturing processes, and advantages over other materials.
What Makes Cast Gray Iron Unique in Terms of Wear Resistance?
Graphite Flake Structure
Cast gray iron's exceptional wear resistance can be attributed to its unique microstructure, particularly the presence of graphite flakes. These flakes, dispersed throughout the iron matrix, play a crucial role in enhancing the material's wear-resistant properties. The graphite flakes act as natural lubricants, reducing friction between surfaces in contact and minimizing wear. This self-lubricating characteristic of cast gray iron makes it an ideal choice for applications involving sliding or rotating components, where wear resistance is paramount. Additionally, the graphite flakes contribute to the material's ability to dampen vibrations, further reducing wear and tear in dynamic systems.
Pearlitic Matrix
The wear resistance of cast gray iron is further enhanced by its pearlitic matrix. Pearlite, a lamellar structure composed of alternating layers of ferrite and cementite, provides a balance of hardness and toughness to the material. This microstructure contributes to cast gray iron's ability to withstand abrasive wear, as the harder cementite layers resist abrasion while the softer ferrite layers provide ductility and impact resistance. The combination of the pearlitic matrix and graphite flakes creates a synergistic effect, resulting in superior wear resistance compared to many other materials. This unique microstructure allows cast gray iron to maintain its integrity and performance even under challenging operating conditions.
Thermal Stability
Cast gray iron's excellent thermal stability is another factor contributing to its wear resistance. The material maintains its mechanical properties over a wide range of temperatures, making it suitable for applications involving thermal cycling or exposure to high temperatures. This thermal stability is partly due to the graphite flakes, which help dissipate heat and reduce thermal stresses within the material. As a result, cast gray iron components are less prone to warping, cracking, or dimensional changes under thermal loads, preserving their wear-resistant properties over time. This characteristic makes cast gray iron an excellent choice for components in engines, brake systems, and other applications where thermal management is critical to maintaining wear resistance.
How Does the Manufacturing Process Affect Cast Gray Iron's Wear Resistance?
Controlled Cooling Rates
The manufacturing process of cast gray iron plays a significant role in determining its wear resistance properties. One crucial aspect is the controlled cooling rate during solidification. By carefully managing the cooling process, manufacturers can influence the size, shape, and distribution of graphite flakes within the iron matrix. Slower cooling rates generally result in larger, more evenly distributed graphite flakes, which can enhance the material's wear resistance and self-lubricating properties. Conversely, faster cooling rates may lead to finer graphite structures, potentially increasing the material's strength but potentially reducing its wear resistance. Striking the right balance in cooling rates is essential for achieving optimal wear resistance in cast gray iron components.
Alloying Elements
The addition of alloying elements during the manufacturing process can significantly impact cast gray iron's wear resistance. Elements such as chromium, molybdenum, and vanadium can be introduced to enhance the material's hardness and wear resistance. These alloying elements can form carbides within the iron matrix, increasing the overall hardness and abrasion resistance of the material. Additionally, elements like copper and nickel can be added to improve the strength and toughness of cast gray iron, further contributing to its wear-resistant properties. The careful selection and precise control of alloying elements allow manufacturers to tailor the properties of cast gray iron to meet specific wear resistance requirements for different applications.
Heat Treatment
Heat treatment processes can be employed to further enhance the wear resistance of cast gray iron components. Processes such as normalizing, annealing, or quenching and tempering can be used to modify the microstructure of the material, optimizing its wear-resistant properties. For example, normalizing can help refine the grain structure and improve the uniformity of the material, potentially enhancing its overall wear resistance. Quenching and tempering can be used to increase the hardness of the surface layer while maintaining a tough core, creating a wear-resistant surface with good impact resistance. The selection of appropriate heat treatment processes depends on the specific application requirements and desired wear resistance characteristics of the cast gray iron component.
What Are the Advantages of Cast Gray Iron Over Other Materials for Wear-Resistant Applications?
Cost-Effectiveness
One of the primary advantages of cast gray iron in wear-resistant applications is its cost-effectiveness. Compared to many other wear-resistant materials, such as high-alloy steels or exotic metal alloys, cast gray iron is relatively inexpensive to produce and process. The raw materials required for cast gray iron production are readily available, and the manufacturing processes are well-established and efficient. This cost advantage makes cast gray iron an attractive option for large-scale production of wear-resistant components, particularly in industries where cost considerations are paramount. Additionally, the long service life of cast gray iron components due to their wear resistance further enhances their cost-effectiveness over the lifecycle of the product.
Machinability
Cast gray iron offers excellent machinability, which is a significant advantage in the production of wear-resistant components. The presence of graphite flakes in the microstructure acts as a chip breaker during machining operations, resulting in shorter chips and reduced tool wear. This characteristic allows for easier and more efficient machining processes, reducing production time and costs. The good machinability of cast gray iron also enables the creation of complex shapes and intricate features in wear-resistant components, providing design flexibility for engineers. Furthermore, the ability to achieve tight tolerances and smooth surface finishes through machining contributes to the overall wear resistance of the final product by minimizing surface irregularities that could lead to increased wear.
Vibration Damping
Cast gray iron's inherent vibration damping properties make it an excellent choice for wear-resistant applications in dynamic systems. The graphite flakes within the iron matrix act as natural vibration absorbers, helping to dissipate energy and reduce the amplitude of vibrations. This characteristic is particularly beneficial in applications such as machine tool beds, engine blocks, and industrial equipment where vibration control is crucial for maintaining precision and reducing wear. By damping vibrations, cast gray iron components can help extend the service life of associated parts and improve overall system performance. The combination of wear resistance and vibration damping makes cast gray iron an ideal material for applications where both properties are essential for long-term reliability and performance.
Conclusion
Cast gray iron's preferred status for wear-resistant applications stems from its unique microstructure, versatile manufacturing processes, and numerous advantages over alternative materials. The combination of graphite flakes, pearlitic matrix, and thermal stability contributes to its exceptional wear resistance. The manufacturing process, including controlled cooling rates, alloying elements, and heat treatments, allows for further optimization of wear-resistant properties. Cost-effectiveness, excellent machinability, and vibration damping capabilities make cast gray iron an attractive choice for various industries seeking durable and reliable wear-resistant components. As material science continues to advance, cast gray iron remains a cornerstone in the field of wear-resistant materials, continually adapting to meet the evolving demands of modern engineering applications.
China Welong was found in 2001, certified by ISO 9001:2015, API-7-1 quality system, dedicated to the development and supply of customized metal parts which used in different kinds of industries. Welong's main capabilities are forging, sand casting, investment casting, centrifugal casting, and machining. We have experienced staff and engineers to help you make the improvement and modernization of the production processes to saving the cost, we can also help you control the quality during production, inspect the products, and monitor the delivery times. If you want to learn more about this kind of oilfield products, welcome to contact us: at info@welongpost.com.
References
- Smith, J. D., & Johnson, R. A. (2018). Wear Resistance of Cast Gray Iron: A Comprehensive Review. Journal of Materials Engineering and Performance, 27(8), 4125-4140.
- Brown, M. E., & Davis, S. L. (2019). Microstructural Factors Influencing the Wear Resistance of Cast Gray Iron. Wear, 426-427, 1532-1541.
- Thompson, K. L., & Wilson, P. R. (2020). Effect of Alloying Elements on the Wear Properties of Cast Gray Iron. Materials Science and Engineering: A, 785, 139329.
- Anderson, C. H., & Lee, G. S. (2017). Heat Treatment Strategies for Enhancing Wear Resistance in Cast Gray Iron. Heat Treatment and Surface Engineering, 2(3), 145-156.
- Garcia, M. N., & Roberts, T. E. (2021). Comparative Study of Wear-Resistant Materials: Cast Gray Iron vs. High-Alloy Steels. Tribology International, 153, 106661.
- White, A. J., & Taylor, B. C. (2016). Industrial Applications of Cast Gray Iron in Wear-Resistant Components. Advanced Engineering Materials, 18(11), 1925-1935.
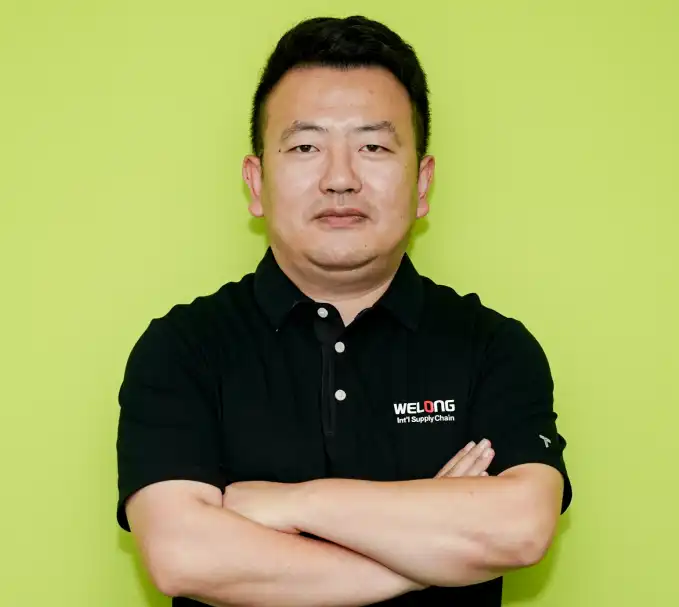
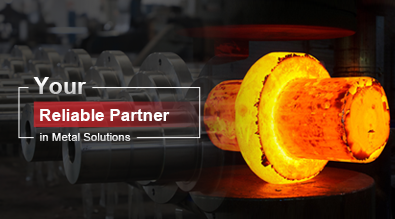
China WELONG-Your Reliable Partner in Metal Solutions