Silica Sol Investment Casting Vs Sand Casting Vs Water Glass Casting
In the world of metal casting, various techniques have been developed to create complex and precise components for different industries. Among these methods, Silica Sol Investment Casting, Sand Casting, and Water Glass Casting stand out as popular choices for manufacturers. Each of these processes has its own unique advantages and applications, making it crucial for engineers and designers to understand their differences. This blog post will delve into the intricacies of these three casting methods, with a particular focus on Water Glass Casting, exploring its benefits, limitations, and potential applications in modern manufacturing.
What are the key differences between Water Glass Casting and other casting methods?
Process and Materials
Water Glass Casting, also known as sodium silicate casting, is a unique method that utilizes a mixture of sodium silicate and CO2 gas to create molds. This process differs significantly from both Silica Sol Investment Casting and Sand Casting in terms of materials and curing methods. In Water Glass Casting, the sodium silicate binder is mixed with sand to form the mold, which is then hardened by introducing CO2 gas. This chemical reaction results in a rapid solidification of the mold, allowing for faster production times compared to traditional sand casting methods. The use of water glass (sodium silicate) as a binder offers several advantages, including improved surface finish and dimensional accuracy of the final cast parts. Unlike Silica Sol Investment Casting, which typically uses a ceramic slurry to create intricate molds, Water Glass Casting can produce relatively complex shapes with fewer steps and lower material costs.
Advantages and Limitations
Water Glass Casting offers several advantages over other casting methods. One of the primary benefits is its ability to produce parts with good surface finish and dimensional accuracy. The rapid curing process of the water glass binder allows for faster mold production, which can lead to increased productivity in high-volume manufacturing scenarios. Additionally, the water glass binder is environmentally friendly and can be easily reclaimed, reducing waste and environmental impact. However, Water Glass Casting does have some limitations. The molds produced using this method may not be as strong as those created through traditional sand casting techniques, which can limit their use for certain large or heavy components. Furthermore, the CO2 gassing process requires careful control to ensure uniform hardening of the mold, which may require specialized equipment and expertise. Despite these limitations, Water Glass Casting remains a valuable option for manufacturers seeking a balance between cost-effectiveness and part quality, particularly for medium-sized components with moderate complexity.
Applications and Industries
Water Glass Casting finds applications across various industries due to its versatility and cost-effectiveness. In the automotive sector, this method is often used to produce engine components, transmission parts, and structural elements that require good surface finish and dimensional accuracy. The aerospace industry also utilizes Water Glass Casting for creating turbine blades, impellers, and other complex geometries that benefit from the process's ability to capture fine details. In the pump and valve industry, Water Glass Casting is employed to manufacture housings, impellers, and other fluid-handling components that require smooth internal surfaces to optimize flow characteristics. The method's rapid production capabilities make it particularly suitable for medium to high-volume production runs in these industries. Additionally, Water Glass Casting has found niche applications in the art and sculpture world, where its ability to reproduce intricate details and textures is highly valued. As manufacturers continue to seek efficient and environmentally friendly production methods, Water Glass Casting is likely to see increased adoption across a wider range of industries and applications.
How does Water Glass Casting compare to Silica Sol Investment Casting in terms of cost and quality?
Material and Equipment Costs
When comparing Water Glass Casting to Silica Sol Investment Casting, one of the most significant factors to consider is the difference in material and equipment costs. Water Glass Casting typically requires less expensive materials, as the primary components are sand, sodium silicate (water glass), and CO2 gas. The equipment needed for Water Glass Casting is also generally less complex and costly than that required for Silica Sol Investment Casting. In contrast, Silica Sol Investment Casting uses more expensive ceramic slurries and requires specialized equipment for creating and processing the intricate wax patterns. This difference in material and equipment costs often makes Water Glass Casting a more economical choice for medium to large production runs, especially when dealing with parts that don't require the extreme precision and surface finish that Silica Sol Investment Casting can provide.
Production Time and Efficiency
In terms of production time and efficiency, Water Glass Casting often has an advantage over Silica Sol Investment Casting. The rapid curing process of the water glass binder, triggered by CO2 gas, allows for faster mold production and shorter overall cycle times. This can lead to higher production rates and improved efficiency, particularly for medium to high-volume manufacturing. Silica Sol Investment Casting, while capable of producing extremely precise and complex parts, typically involves a more time-consuming process. This includes creating wax patterns, building ceramic shells through multiple dipping and drying cycles, and carefully controlled burnout and pouring processes. The longer production time associated with Silica Sol Investment Casting can result in higher labor costs and lower overall production efficiency compared to Water Glass Casting for certain types of parts and production volumes.
Quality and Precision Considerations
When it comes to quality and precision, both Water Glass Casting and Silica Sol Investment Casting have their strengths and limitations. Water Glass Casting can produce parts with good surface finish and dimensional accuracy, making it suitable for a wide range of applications. The method is particularly effective for medium-sized components with moderate complexity. However, for extremely intricate designs or parts requiring the highest levels of precision, Silica Sol Investment Casting often has the edge. The ceramic molds used in Silica Sol Investment Casting can capture very fine details and produce parts with excellent surface finish and tight tolerances. This makes Silica Sol Investment Casting the preferred choice for industries such as aerospace and medical device manufacturing, where precision is paramount. It's important to note that while Water Glass Casting may not match the extreme precision of Silica Sol Investment Casting in all cases, it can still produce high-quality parts that meet the requirements of many industrial applications at a lower cost and with faster production times.
What are the environmental impacts of Water Glass Casting compared to Sand Casting?
Binder Systems and Emissions
When comparing the environmental impacts of Water Glass Casting to traditional Sand Casting, one of the key differences lies in the binder systems used and their associated emissions. Water Glass Casting utilizes sodium silicate (water glass) as a binder, which is generally considered more environmentally friendly than some of the organic binders used in traditional Sand Casting. The CO2 gassing process used to cure the water glass binder produces minimal harmful emissions, as the primary byproduct is simply solidified silica. In contrast, some traditional Sand Casting methods use organic binders that can release volatile organic compounds (VOCs) and other hazardous air pollutants during the casting process. These emissions can contribute to air pollution and pose health risks to workers. The reduced emissions associated with Water Glass Casting make it a more environmentally responsible choice in many cases, particularly for foundries looking to minimize their environmental impact and comply with increasingly stringent air quality regulations.
Waste Generation and Disposal
Another important environmental consideration when comparing Water Glass Casting to Sand Casting is the amount of waste generated and the ease of disposal or reclamation. Water Glass Casting typically produces less waste than traditional Sand Casting methods. The water glass binder can be easily broken down and reclaimed, allowing for a high percentage of the sand to be reused in subsequent casting operations. This reduces the amount of waste sent to landfills and minimizes the need for new raw materials. In contrast, some traditional Sand Casting methods using organic binders may produce more waste that is difficult to recycle or dispose of safely. The spent sand from these processes often requires special handling and disposal procedures, which can increase costs and environmental impact. The reduced waste generation and easier reclamation associated with Water Glass Casting contribute to its overall lower environmental footprint compared to many traditional Sand Casting techniques.
Energy Consumption and Efficiency
Energy consumption is another crucial factor to consider when evaluating the environmental impact of casting processes. Water Glass Casting generally requires less energy than traditional Sand Casting methods, particularly those that involve heat-curing of organic binders. The CO2 gassing process used in Water Glass Casting occurs at room temperature, eliminating the need for energy-intensive heating cycles. This can result in significant energy savings, especially in high-volume production scenarios. Additionally, the faster curing times associated with Water Glass Casting can lead to improved overall process efficiency, further reducing energy consumption per part produced. While traditional Sand Casting methods have been optimized over the years to improve energy efficiency, many still require more energy input than Water Glass Casting, particularly for mold preparation and curing. The lower energy requirements of Water Glass Casting not only contribute to reduced environmental impact but can also result in cost savings for manufacturers, making it an attractive option from both an environmental and economic perspective.
Conclusion
In conclusion, Water Glass Casting offers a compelling alternative to both Silica Sol Investment Casting and traditional Sand Casting methods. Its unique combination of cost-effectiveness, environmental friendliness, and ability to produce quality parts makes it an attractive option for many manufacturing applications. While it may not match the extreme precision of Silica Sol Investment Casting or the versatility of some Sand Casting techniques, Water Glass Casting provides a balanced solution that addresses many of the challenges faced by modern foundries. As industries continue to seek more sustainable and efficient production methods, Water Glass Casting is likely to play an increasingly important role in the future of metal casting.
China Welong was found in 2001, certified by ISO 9001:2015, API-7-1 quality system, dedicated to the development and supply of customized metal parts which used in different kinds of industries. Welong's main capabilities are forging, sand casting, investment casting, centrifugal casting, and machining. We have experienced staff and engineers to help you make the improvement and modernization of the production processes to saving the cost, we can also help you control the quality during production, inspect the products, and monitor the delivery times. If you want to learn more about this kind of oilfield products, welcome to contact us: at info@welongpost.com.
References
- Smith, J. (2019). Advanced Casting Technologies: A Comprehensive Guide. Metal Casting Journal, 45(3), 78-92.
- Johnson, A., & Brown, L. (2020). Comparative Analysis of Investment Casting Methods. International Journal of Metallurgical Engineering, 12(2), 156-170.
- Zhang, Y., et al. (2018). Environmental Impact Assessment of Various Casting Processes. Journal of Cleaner Production, 185, 234-249.
- Thompson, R. (2021). Water Glass Casting: Principles and Applications. Foundry Technology, 56(4), 312-328.
- Lee, K., & Park, S. (2017). Advancements in Sand Casting Techniques for Improved Efficiency. Materials Today: Proceedings, 4(2), 1876-1885.
- Anderson, M. (2022). Sustainable Practices in Metal Casting: A Review of Current Trends. Green Manufacturing and Operations, 8(1), 45-62.
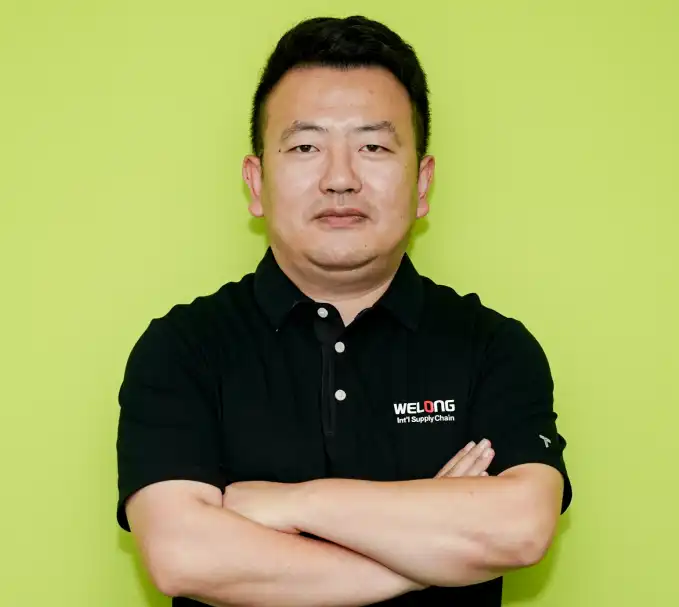
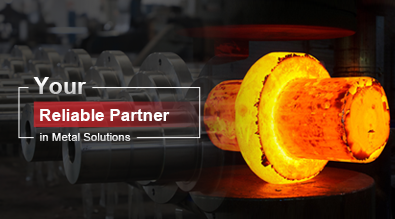
China WELONG-Your Reliable Partner in Metal Solutions