Common Casting Defects in Cast Gray Iron and How to Prevent Them
Cast gray iron is a widely used material in various industries due to its excellent mechanical properties and cost-effectiveness. However, like any casting process, the production of cast gray iron components can be prone to defects that may compromise the quality and performance of the final product. In this blog post, we will explore common casting defects encountered in cast gray iron production and discuss effective prevention strategies. Understanding these defects and their causes is crucial for manufacturers to improve their casting processes and produce high-quality gray iron components.
What are the most common porosity defects in cast gray iron?
Gas Porosity
Gas porosity is one of the most prevalent defects in cast gray iron. This type of porosity occurs when gases become trapped within the solidifying metal, resulting in small, rounded voids scattered throughout the casting. In cast gray iron, gas porosity can be caused by several factors, including excessive moisture in the molding sand, inadequate venting of the mold, or the presence of volatile elements in the metal charge. To prevent gas porosity in cast gray iron, foundries should ensure proper drying of molding sand, implement effective mold venting techniques, and carefully control the composition of the metal charge. Additionally, maintaining the correct pouring temperature and using degassing treatments can help minimize gas entrapment during solidification.
Shrinkage Porosity
Shrinkage porosity is another common defect in cast gray iron that occurs due to the natural contraction of the metal as it solidifies. This type of porosity manifests as irregularly shaped voids, often concentrated in thicker sections of the casting where solidification occurs last. In cast gray iron, shrinkage porosity can be particularly challenging due to the material's tendency to form a solid skin while the interior remains liquid. To mitigate shrinkage porosity in cast gray iron, foundries should focus on optimizing gating and risering systems to ensure proper directional solidification. Implementing chills or using exothermic sleeves can help promote uniform cooling and reduce the likelihood of shrinkage defects. Furthermore, careful control of the carbon equivalent and inoculation practices can influence the solidification behavior of cast gray iron and minimize shrinkage-related issues.
Microshrinkage
Microshrinkage is a subtle yet significant defect that can affect cast gray iron components. Unlike larger shrinkage cavities, microshrinkage appears as a network of small, interconnected voids that can compromise the mechanical properties and pressure tightness of the casting. In cast gray iron, microshrinkage is often associated with inadequate feeding of isolated sections or poor control of the graphite morphology. To prevent microshrinkage in cast gray iron, foundries should pay close attention to part design, ensuring that all sections can be adequately fed during solidification. Optimizing the carbon equivalent and silicon content can promote the formation of graphite flakes that compensate for shrinkage. Additionally, proper inoculation practices and controlled cooling rates can help achieve a uniform graphite structure throughout the casting, reducing the risk of microshrinkage defects.
How does graphite structure affect the properties of cast gray iron?
Flake Graphite Morphology
The graphite structure plays a crucial role in determining the properties of cast gray iron. Flake graphite morphology is the most common form found in conventional gray iron castings. The shape, size, and distribution of these graphite flakes significantly influence the material's mechanical and thermal characteristics. In cast gray iron with flake graphite, the interconnected nature of the graphite particles provides excellent thermal conductivity and vibration damping properties. However, the flake structure can also act as stress concentrators, potentially reducing the material's tensile strength and ductility. To optimize the flake graphite morphology in cast gray iron, foundries must carefully control the composition, particularly the carbon and silicon content, as well as the cooling rate during solidification. Proper inoculation practices are also essential to promote the formation of numerous, evenly distributed graphite flakes throughout the casting.
Chunky Graphite Formation
Chunky graphite is an undesirable morphology that can occur in cast gray iron, particularly in thick sections or areas with slow cooling rates. This type of graphite structure appears as interconnected, coarse particles that can severely compromise the mechanical properties of the casting. The formation of chunky graphite in cast gray iron is often associated with high carbon equivalents, excessive amounts of certain trace elements (such as cerium or calcium), or inadequate inoculation practices. To prevent chunky graphite formation in cast gray iron, foundries should carefully control the chemical composition of the melt, paying particular attention to the balance of graphite-promoting and carbide-stabilizing elements. Implementing appropriate cooling strategies for thick sections, such as the use of chills or controlled solidification techniques, can help avoid the conditions that favor chunky graphite growth. Additionally, optimizing the inoculation process and using specially formulated inoculants can promote the formation of desirable graphite structures and suppress chunky graphite formation.
Compacted Graphite Transition
While not strictly a defect, the unintended formation of compacted (or vermicular) graphite in cast gray iron can lead to unexpected changes in material properties. Compacted graphite iron (CGI) exhibits a unique graphite structure that falls between flake graphite and spheroidal graphite, offering a combination of properties that can be advantageous in certain applications. However, when producing conventional cast gray iron, the inadvertent formation of compacted graphite can result in variations in mechanical properties and machinability. The transition to compacted graphite in cast gray iron is often influenced by factors such as high magnesium or rare earth element content, specific cooling conditions, or the presence of certain impurities. To prevent unintended compacted graphite formation in cast gray iron, foundries should maintain strict control over the chemical composition of the melt, particularly the levels of magnesium and rare earth elements. Careful monitoring of the sulfur content and implementing appropriate desulfurization practices can also help maintain the desired flake graphite structure. Furthermore, optimizing the inoculation process and cooling rates can ensure consistent graphite morphology throughout the casting.
What are the best practices for controlling inclusions in cast gray iron?
Slag Inclusions
Slag inclusions are non-metallic impurities that can become entrapped in cast gray iron during the melting and pouring processes. These inclusions can significantly impact the mechanical properties, machinability, and surface finish of the final casting. In cast gray iron production, slag inclusions often originate from reactions between the molten metal and furnace lining, ladle refractories, or oxidation products formed during melting. To minimize slag inclusions in cast gray iron, foundries should implement rigorous melt preparation and handling practices. This includes proper cleaning and maintenance of furnaces and ladles, as well as the use of effective slag removal techniques such as skimming or the application of slag coagulants. Implementing a well-designed gating system with slag traps can help prevent slag from entering the mold cavity during pouring. Additionally, maintaining the correct pouring temperature and using ceramic foam filters in the gating system can further reduce the risk of slag inclusions in cast gray iron castings.
Sand Inclusions
Sand inclusions are a common defect in cast gray iron components produced using sand mold casting techniques. These defects occur when particles from the molding sand become dislodged and are incorporated into the casting during the pouring and solidification processes. Sand inclusions can lead to surface defects, reduced mechanical properties, and difficulties in machining. In cast gray iron production, sand inclusions may result from poor sand quality, inadequate mold compaction, or excessive turbulence during pouring. To prevent sand inclusions in cast gray iron, foundries should focus on maintaining high-quality molding sand with proper grain size distribution and binder content. Implementing effective sand preparation and testing procedures can help ensure consistent sand properties. Careful mold making techniques, including proper compaction and the use of facing sands or mold coatings, can improve the mold surface integrity. Designing gating systems that minimize turbulence and employing pouring practices that reduce metal velocity can also help prevent sand erosion and inclusion formation in cast gray iron castings.
Refractory Inclusions
Refractory inclusions in cast gray iron are typically the result of erosion or spalling of refractory materials used in furnaces, ladles, or other metal handling equipment. These inclusions can cause similar issues to slag inclusions, potentially compromising the casting's integrity and performance. In cast gray iron production, refractory inclusions may be more prevalent when using older or poorly maintained equipment, or when subjecting refractories to thermal shock or chemical attack. To minimize refractory inclusions in cast gray iron, foundries should implement a comprehensive refractory management program. This includes regular inspection and maintenance of furnace linings, ladles, and pouring equipment. Selecting appropriate refractory materials that are compatible with the cast gray iron composition and operating conditions is crucial. Implementing proper preheating procedures for ladles and transfer vessels can help reduce thermal shock and minimize refractory erosion. Additionally, using ceramic foam filters in the gating system can help capture any refractory particles that may enter the melt stream during pouring, further reducing the risk of inclusions in the final cast gray iron component.
Conclusion
Understanding and preventing common casting defects in cast gray iron is crucial for producing high-quality components with consistent properties. By addressing issues such as porosity, graphite structure control, and inclusion prevention, foundries can significantly improve their casting processes and product quality. Implementing best practices in melt preparation, mold design, and process control is essential for minimizing defects and achieving optimal performance in cast gray iron components. As the industry continues to evolve, ongoing research and development in casting technologies and materials science will undoubtedly lead to further improvements in cast gray iron production, enabling manufacturers to meet the ever-increasing demands for high-performance, cost-effective components across various industries.
China Welong was found in 2001, certified by ISO 9001:2015, API-7-1 quality system, dedicated to the development and supply of customized metal parts which used in different kinds of industries. Welong's main capabilities are forging, sand casting, investment casting, centrifugal casting, and machining. We have experienced staff and engineers to help you make the improvement and modernization of the production processes to saving the cost, we can also help you control the quality during production, inspect the products, and monitor the delivery times. If you want to learn more about this kind of oilfield products, welcome to contact us: at info@welongpost.com.
References
- Brown, J. R. (2000). Foseco Ferrous Foundryman's Handbook. Butterworth-Heinemann.
- Campbell, J. (2015). Complete Casting Handbook: Metal Casting Processes, Metallurgy, Techniques and Design. Butterworth-Heinemann.
- Stefanescu, D. M. (2009). Science and Engineering of Casting Solidification. Springer.
- American Foundry Society. (2015). Casting Defects Handbook: Iron & Steel. AFS.
- Agarwal, R. L., & Banga, T. R. (2016). Foundry Technology. Khanna Publishers.
- Ductile Iron Society. (2013). Ductile Iron Quality Control Manual. DIS.

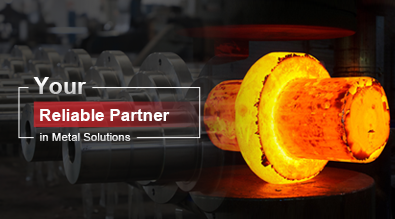
China WELONG-Your Reliable Partner in Metal Solutions