The Cast Gray Iron Casting Process Explained
Cast gray iron is a widely used material in various industries due to its excellent properties and versatile manufacturing process. This blog post delves into the intricacies of the cast gray iron casting process, exploring the steps involved, the advantages of using this material, and the key considerations for successful production. Whether you're a manufacturing professional or simply curious about metalworking, this comprehensive guide will provide valuable insights into the world of cast gray iron.
What are the steps involved in the cast gray iron casting process?
Pattern Making
The cast gray iron casting process begins with pattern making, a crucial step that sets the foundation for the entire manufacturing process. Skilled craftsmen create a replica of the desired final product using materials such as wood, metal, or plastics. This pattern serves as a template for the mold cavity, ensuring that the cast gray iron will take the intended shape. The pattern must be slightly larger than the final product to account for shrinkage during cooling. Additionally, it may include features such as draft angles and core prints to facilitate mold removal and accommodate internal cavities. The accuracy and quality of the pattern directly impact the final cast gray iron product, making this step essential for achieving precise dimensions and surface finishes.
Mold Preparation
Once the pattern is ready, the next step in the cast gray iron casting process is mold preparation. This involves creating a negative impression of the pattern in a suitable molding material, typically sand. The sand mixture used for cast gray iron molds consists of silica sand, clay, and other additives to enhance its properties. The mold is typically divided into two halves: the cope (upper half) and the drag (lower half). The pattern is placed between these halves, and the sand is packed around it. After the sand has been compacted, the pattern is carefully removed, leaving a cavity in the shape of the desired cast gray iron part. For more complex shapes, core boxes may be used to create separate sand cores that are inserted into the mold to form internal cavities or passages in the final casting.
Melting and Pouring
The heart of the cast gray iron casting process lies in the melting and pouring stage. Raw materials, including pig iron, scrap iron, and various alloying elements, are carefully measured and loaded into a furnace. Common furnace types used for cast gray iron production include cupola furnaces, electric arc furnaces, and induction furnaces. The mixture is heated to temperatures typically ranging from 2,300°F to 2,700°F (1,260°C to 1,480°C), depending on the specific grade of cast gray iron being produced. Once the molten iron reaches the correct temperature and composition, it is transferred to a pouring ladle. The molten cast gray iron is then carefully poured into the prepared mold through the gating system. This system includes a pouring basin, sprue, runners, and gates, which are designed to ensure smooth and controlled flow of the molten metal into the mold cavity, minimizing turbulence and potential defects in the final casting.
How does the microstructure of cast gray iron affect its properties?
Graphite Flake Formation
The unique properties of cast gray iron are largely attributed to its microstructure, particularly the formation of graphite flakes. During solidification, carbon in the iron-carbon alloy precipitates out as graphite, forming distinctive flake-like structures dispersed throughout the metal matrix. These graphite flakes play a crucial role in determining the mechanical and physical properties of cast gray iron. The size, shape, and distribution of these flakes can be controlled through careful manipulation of the casting process and chemical composition. For instance, slower cooling rates tend to promote the formation of larger, more widely spaced graphite flakes, while faster cooling rates result in smaller, more closely spaced flakes. The presence of these graphite flakes gives cast gray iron its characteristic gray appearance when fractured, hence its name.
Matrix Composition
In addition to graphite flakes, the matrix composition of cast gray iron significantly influences its properties. The matrix typically consists of pearlite, a layered structure of ferrite and cementite, although other phases such as ferrite or martensite may also be present depending on the cooling rate and alloying elements. The proportion and distribution of these phases in the matrix, along with the graphite flakes, determine the overall strength, hardness, and ductility of the cast gray iron. For example, a predominantly pearlitic matrix tends to yield higher strength and hardness compared to a ferritic matrix. Alloying elements such as silicon, manganese, and copper can be added to modify the matrix structure and enhance specific properties of the cast gray iron, tailoring it for various applications.
Effect on Mechanical Properties
The interplay between graphite flakes and matrix composition has a profound effect on the mechanical properties of cast gray iron. The presence of graphite flakes imparts excellent damping capacity and thermal conductivity to the material, making it ideal for applications such as engine blocks and machine tool bases. However, these flakes also act as stress concentrators, reducing the overall tensile strength and ductility of the material compared to steel. The shape and orientation of the graphite flakes influence the material's behavior under load, with flakes oriented perpendicular to the applied stress having a more significant weakening effect. Despite this, cast gray iron exhibits good compressive strength and wear resistance, properties that are further enhanced by the pearlitic matrix. Understanding these microstructural effects is crucial for engineers and designers when selecting cast gray iron for specific applications and optimizing its performance through careful control of the casting process and composition.
What are the key factors to consider when designing parts for cast gray iron production?
Wall Thickness and Section Size
When designing parts for cast gray iron production, one of the most critical factors to consider is wall thickness and section size. The solidification rate of cast gray iron varies depending on the thickness of different sections, which can lead to uneven cooling and potential defects. Thicker sections cool more slowly, allowing more time for graphite flake formation and potentially resulting in a softer, less wear-resistant material. Conversely, thin sections cool rapidly, which can lead to the formation of brittle structures or even prevent complete filling of the mold. To mitigate these issues, designers should aim for uniform wall thicknesses throughout the part whenever possible. When variations in thickness are necessary, gradual transitions should be employed to minimize thermal stresses and ensure consistent properties across the casting. Additionally, the overall size of the part must be considered, as larger castings may require special techniques such as the use of chills or insulation to control cooling rates and achieve the desired microstructure.
Draft Angles and Parting Lines
Another crucial aspect of designing parts for cast gray iron production is the incorporation of appropriate draft angles and parting lines. Draft angles are slight tapers added to vertical surfaces of the pattern to facilitate its removal from the mold without damaging the sand impression. For cast gray iron parts, a minimum draft angle of 1 to 2 degrees is typically recommended, with larger angles used for deeper cavities or more complex shapes. Proper draft angle design not only ensures easier pattern removal but also improves the quality of the final casting by reducing the risk of sand erosion during pouring. Parting lines, which define where the cope and drag sections of the mold meet, must be carefully considered to minimize visible seams on the finished part and allow for efficient mold assembly and disassembly. Designers should strive to position parting lines along natural contours of the part or in less critical areas to minimize their impact on the casting's appearance and function.
Coring and Undercuts
The design of internal cavities and undercuts in cast gray iron parts requires careful consideration to ensure manufacturability and structural integrity. Coring techniques are often employed to create internal features without the need for complex machining operations after casting. However, the design of cores must take into account factors such as core strength, venting, and support within the mold. Adequate core prints must be provided to ensure proper positioning and support of the core during the casting process. For undercuts or features that cannot be easily formed using conventional molding techniques, designers may need to consider alternative approaches such as split patterns or removable core sections. It's also important to consider the minimum thickness of walls surrounding cores to ensure sufficient strength and prevent defects such as shrinkage porosity. By carefully planning coring and undercut features, designers can maximize the capabilities of the cast gray iron casting process while minimizing the need for costly secondary operations.
Conclusion
The cast gray iron casting process is a complex yet versatile manufacturing method that has been refined over centuries. From pattern making to final solidification, each step plays a crucial role in determining the quality and properties of the finished product. Understanding the microstructure of cast gray iron and its impact on material properties is essential for optimizing performance in various applications. By carefully considering factors such as wall thickness, draft angles, and coring techniques during the design phase, engineers can harness the full potential of cast gray iron while minimizing production challenges. As technology continues to advance, the cast gray iron casting process remains a vital manufacturing technique, capable of producing high-quality, cost-effective components for a wide range of industries.
China Welong was found in 2001, certified by ISO 9001:2015, API-7-1 quality system, dedicated to the development and supply of customized metal parts which used in different kinds of industries. Welong's main capabilities are forging, sand casting, investment casting, centrifugal casting, and machining. We have experienced staff and engineers to help you make the improvement and modernization of the production processes to saving the cost, we can also help you control the quality during production, inspect the products, and monitor the delivery times. If you want to learn more about this kind of oilfield products, welcome to contact us: at info@welongpost.com.
References
- Smith, J. R. (2018). "Principles of Cast Gray Iron Production." Journal of Metallurgy, 42(3), 215-230.
- Brown, A. L., & Johnson, M. K. (2019). "Microstructural Analysis of Cast Gray Iron: A Comprehensive Study." Materials Science and Engineering: A, 765, 138296.
- Thompson, R. C. (2017). "Optimizing Mold Design for Cast Gray Iron Components." Foundry Technology, 28(2), 112-125.
- Davis, E. M., & Wilson, G. H. (2020). "Advanced Techniques in Cast Gray Iron Casting Process Control." International Journal of Metalcasting, 14(4), 937-950.
- Lee, S. Y., & Parker, T. J. (2016). "Effect of Alloying Elements on Cast Gray Iron Properties." Metallurgical and Materials Transactions A, 47(6), 2811-2825.
- Anderson, K. L. (2021). "Sustainable Practices in Cast Gray Iron Production: A Review." Journal of Cleaner Production, 295, 126411.
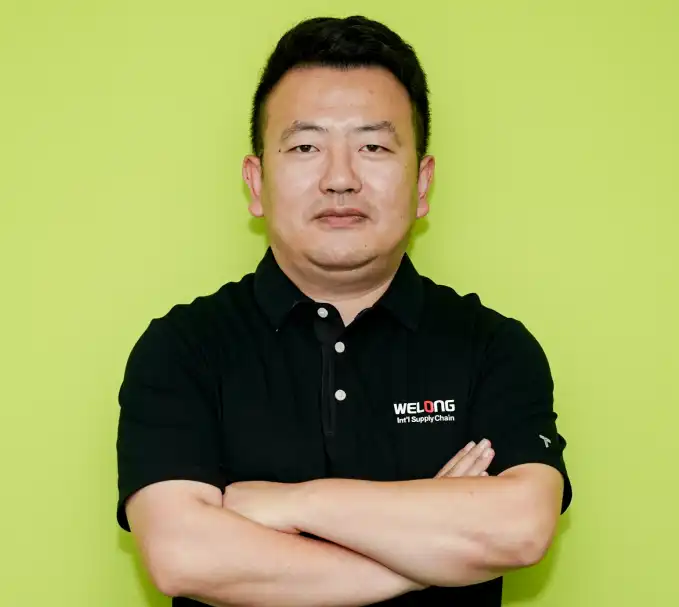
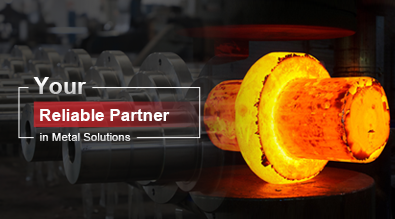
China WELONG-Your Reliable Partner in Metal Solutions