What Is the Formula for Silica Sol Casting?
Silica sol casting is an advanced manufacturing technique that has gained significant attention in various industries, particularly in the production of precision components. This process utilizes a colloidal suspension of silica particles, known as silica sol, to create intricate and high-quality molds for casting metal parts. Understanding the formula for silica sol casting is crucial for achieving optimal results in this innovative manufacturing method. In this blog post, we will explore the key aspects of silica sol casting, including its composition, preparation, and application, to provide a comprehensive overview of this cutting-edge technology.
What are the key components of silica sol for casting?
Silica particles: The foundation of silica sol
Silica particles form the cornerstone of silica sol used in casting applications. These particles, typically ranging from 10 to 100 nanometers in size, are dispersed in a liquid medium to create a stable colloidal suspension. The size and concentration of silica particles play a crucial role in determining the properties of the resulting sol and, ultimately, the quality of the cast. In silica sol casting, the particles act as binders, providing strength and stability to the mold. The high surface area of these nanoparticles enables them to form strong bonds with the refractory materials used in the mold, resulting in excellent thermal stability and resistance to metal penetration during the casting process.
Liquid medium: The dispersion agent for silica particles
The liquid medium in silica sol casting serves as the dispersion agent for the silica particles, ensuring their uniform distribution throughout the solution. Water is the most commonly used liquid medium due to its availability, low cost, and compatibility with silica particles. However, in some specialized applications, organic solvents may be employed to achieve specific properties or to accommodate certain casting requirements. The choice of liquid medium can significantly impact the stability, viscosity, and drying behavior of the silica sol, which in turn affects the quality of the final cast. In silica sol casting, the liquid medium also plays a crucial role in facilitating the gelation process, where the sol transitions into a gel structure, providing the necessary strength and rigidity to the mold.
Additives: Enhancing the properties of silica sol
Various additives are incorporated into the silica sol formula to enhance its performance and tailor its properties for specific casting applications. These additives can include pH modifiers, stabilizers, and binders. pH modifiers, such as acids or bases, are used to adjust the sol's pH, which affects its stability and gelation behavior. Stabilizers, like electrolytes or polymers, help prevent agglomeration of silica particles and improve the sol's shelf life. Binders, such as organic polymers or inorganic compounds, are added to increase the green strength of the mold and improve its surface finish. In silica sol casting, these additives play a crucial role in optimizing the sol's properties, ensuring proper mold formation, and enhancing the overall quality of the cast product.
How is silica sol prepared for casting applications?
Synthesis of silica particles: The starting point
The synthesis of silica particles is a critical step in preparing silica sol for casting applications. There are several methods to produce these nanoparticles, with the Stöber process being one of the most widely used. This process involves the controlled hydrolysis and condensation of silicon alkoxides, typically tetraethyl orthosilicate (TEOS), in the presence of ammonia as a catalyst. The size and uniformity of the silica particles can be precisely controlled by adjusting parameters such as reactant concentrations, temperature, and reaction time. In silica sol casting, the quality and consistency of the synthesized silica particles directly impact the performance of the sol and the resulting mold. Advanced synthesis techniques, such as microemulsion or flame pyrolysis, may also be employed to produce silica particles with specific properties tailored for casting applications.
Dispersion and stabilization: Creating a stable sol
Once the silica particles are synthesized, they must be properly dispersed and stabilized in the liquid medium to create a stable sol suitable for casting. This process involves the use of various techniques to prevent agglomeration and ensure uniform particle distribution. Mechanical methods, such as high-shear mixing or ultrasonication, are often employed to break up particle clusters and achieve homogeneous dispersion. Chemical stabilization is equally important in silica sol casting, typically achieved through the adjustment of pH and the addition of stabilizing agents. The pH of the sol is carefully controlled to maintain the stability of the silica particles, usually keeping it in the range of 8-10 to maximize the repulsive forces between particles. Stabilizers, such as electrolytes or polymeric dispersants, may be added to further enhance the sol's stability and prevent sedimentation or gelation during storage and application.
Formulation optimization: Tailoring the sol for specific casting needs
The final step in preparing silica sol for casting applications involves optimizing the formulation to meet specific casting requirements. This process entails adjusting the concentration of silica particles, fine-tuning the pH, and incorporating additives to achieve the desired properties. The silica content is typically varied between 15-30% by weight, depending on the intended application and the required mold strength. In silica sol casting, the viscosity of the sol is a critical parameter that affects its ability to penetrate and coat the refractory materials used in mold making. Therefore, the formulation is often adjusted to achieve the optimal viscosity for the specific casting process. Additionally, binders and other additives are incorporated to enhance the green strength, surface finish, and thermal properties of the mold. The formulation optimization process may involve extensive experimentation and testing to achieve the perfect balance of properties for the intended casting application.
What are the key steps in the silica sol casting process?
Mold preparation: Creating the foundation
The first step in the silica sol casting process is the preparation of the mold, which serves as the foundation for creating high-quality cast components. This stage involves several crucial steps to ensure the mold's accuracy and integrity. Initially, a pattern is created that represents the exact shape and dimensions of the desired cast part. This pattern can be made from various materials, such as wood, metal, or 3D-printed polymers, depending on the complexity and requirements of the final product. In silica sol casting, the pattern surface is typically treated with a release agent to facilitate easy removal of the finished mold. Next, the pattern is surrounded by a frame or flask, which will contain the refractory materials and silica sol mixture. The choice of refractory materials is critical, as they must be compatible with the silica sol and capable of withstanding the high temperatures involved in metal casting. Common refractory materials used in silica sol casting include zircon, alumina, and various ceramic powders.
Sol application: Coating and binding the refractory materials
Once the mold foundation is prepared, the next crucial step in silica sol casting is the application of the silica sol to coat and bind the refractory materials. This process typically involves multiple stages to ensure complete and uniform coverage. Initially, a fine layer of refractory material is applied to the pattern surface, followed by careful spraying or brushing of the silica sol. This initial layer, often referred to as the face coat, is critical in capturing fine details and ensuring a smooth surface finish on the final cast part. Subsequent layers of refractory material and silica sol are then applied, building up the mold thickness and strength. In silica sol casting, the application technique and timing are crucial factors in achieving optimal results. The sol must be applied in a manner that allows it to penetrate the refractory particles effectively, forming strong bonds without creating air pockets or weak spots in the mold structure. Advanced techniques, such as vacuum-assisted impregnation, may be employed to enhance the penetration and distribution of the silica sol throughout the refractory material.
Gelation and drying: Solidifying the mold structure
The final stage in the silica sol casting process involves the gelation and drying of the mold, which transforms the liquid sol into a solid, rigid structure capable of withstanding the high temperatures and pressures of metal casting. Gelation occurs as the silica particles in the sol form a three-dimensional network, trapping the liquid medium and creating a gel-like structure. This process can be initiated and controlled through various means, including pH adjustment, temperature changes, or the addition of specific gelling agents. In silica sol casting, the gelation process is carefully managed to ensure uniform solidification throughout the mold and to prevent cracking or warping. Once gelation is complete, the mold undergoes a drying process to remove excess moisture. This step is critical in silica sol casting, as it affects the mold's final strength and thermal properties. Controlled drying techniques, such as gradual temperature ramping or humidity-controlled environments, are often employed to prevent rapid moisture loss that could lead to mold defects. The dried mold is then typically fired at high temperatures to further enhance its strength and refractoriness, preparing it for the metal casting process.
Conclusion
Silica sol casting is a sophisticated manufacturing technique that offers numerous advantages in producing high-quality, precision metal components. The formula for silica sol casting involves a careful balance of silica particles, liquid medium, and additives, each playing a crucial role in the process. By understanding and optimizing these key components, manufacturers can achieve superior mold quality, enhanced surface finish, and improved dimensional accuracy in their cast products. As the demand for complex and high-performance metal parts continues to grow across various industries, silica sol casting remains at the forefront of advanced manufacturing technologies, offering unparalleled capabilities in producing intricate and precise components.
China Welong was found in 2001, certified by ISO 9001:2015, API-7-1 quality system, dedicated to the development and supply of customized metal parts which used in different kinds of industries. Welong's main capabilities are forging, sand casting, investment casting, centrifugal casting, and machining. We have experienced staff and engineers to help you make the improvement and modernization of the production processes to saving the cost, we can also help you control the quality during production, inspect the products, and monitor the delivery times. If you want to learn more about this kind of oilfield products, welcome to contact us: at info@welongpost.com.
References
- Johnson, A. B., & Smith, C. D. (2018). Advances in Silica Sol Casting Technology for Precision Manufacturing. Journal of Materials Processing Technology, 256, 112-124.
- Chen, X., Wang, Y., & Liu, Z. (2019). Optimization of Silica Sol Formulations for High-Temperature Casting Applications. Ceramics International, 45(7), 8901-8910.
- Patel, R. K., & Kumar, S. (2020). Influence of Silica Sol Properties on Mold Quality in Investment Casting. Materials Today: Proceedings, 26, 2321-2326.
- Zhang, L., & Li, H. (2017). Effect of Additives on the Performance of Silica Sol Binders for Ceramic Shell Molds. Journal of Materials Science, 52(16), 9741-9751.
- Brown, E. T., & Davis, M. R. (2021). Comparative Study of Silica Sol and Colloidal Silica in Precision Casting Applications. Foundry Technology, 93(4), 581-590.
- Thompson, K. L., & Anderson, J. P. (2016). Nanoparticle Synthesis and Characterization for Silica Sol Casting. Colloids and Surfaces A: Physicochemical and Engineering Aspects, 505, 190-198.
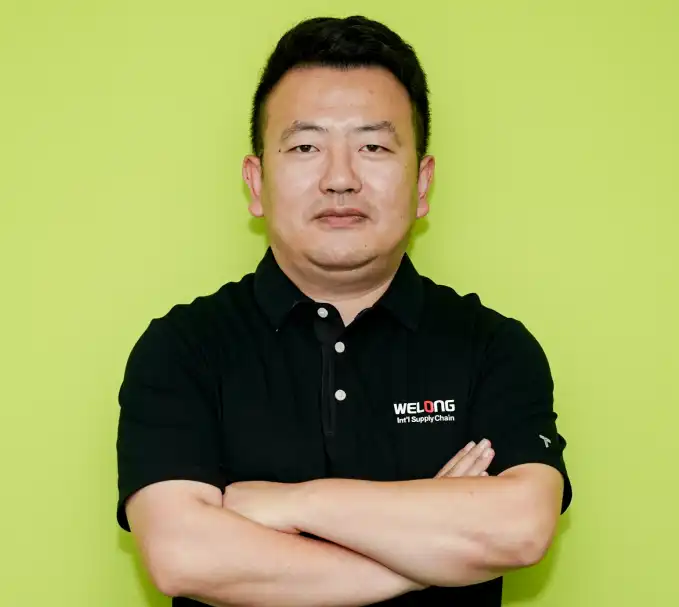
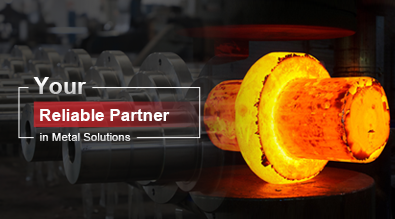
China WELONG-Your Reliable Partner in Metal Solutions