Exploring the Mechanical Properties of Cast Gray Iron
Cast gray iron is a versatile and widely used material in various industries due to its unique mechanical properties. This blog post delves into the characteristics that make cast gray iron an essential material in manufacturing and engineering applications. We'll explore its strength, durability, and performance under different conditions, providing insights into why it remains a popular choice for many industrial components.
What are the key mechanical properties of cast gray iron?
Tensile Strength and Ductility
Cast gray iron exhibits remarkable tensile strength, making it suitable for applications that require resistance to pulling forces. The material's graphite flakes, which are dispersed throughout its microstructure, contribute to its unique properties. These flakes act as stress concentrators, influencing the material's behavior under tension. While cast gray iron's tensile strength is generally lower than that of steel, it still provides adequate performance for many applications. The ductility of cast gray iron is relatively low compared to other ferrous materials, which means it has limited ability to deform plastically before fracture. This characteristic is due to the presence of graphite flakes, which create discontinuities in the iron matrix. However, this apparent disadvantage can be beneficial in certain applications where vibration damping is crucial.
Compressive Strength and Hardness
One of the standout features of cast gray iron is its exceptional compressive strength. The material can withstand significant compressive loads without failing, making it ideal for components subjected to high pressures or weight-bearing applications. The graphite flakes in cast gray iron contribute to its compressive strength by acting as lubricants under stress, allowing for better load distribution. This property is particularly valuable in applications such as machine tool beds, engine blocks, and heavy equipment components. In terms of hardness, cast gray iron generally exhibits good resistance to wear and abrasion. The hardness can be further enhanced through heat treatment processes, allowing manufacturers to tailor the material's properties to specific requirements.
Thermal Conductivity and Damping Capacity
Cast gray iron possesses excellent thermal conductivity, which makes it an ideal material for applications involving heat transfer. This property is particularly useful in automotive and industrial equipment where efficient heat dissipation is crucial. The graphite flakes in the iron matrix act as efficient heat conductors, allowing for rapid and uniform heat distribution throughout the material. This characteristic contributes to cast gray iron's popularity in applications such as brake rotors, cookware, and heat exchanger components. Additionally, cast gray iron exhibits superior damping capacity, which is its ability to absorb and dissipate vibrational energy. This property is attributed to the graphite flakes, which act as natural dampers within the material's structure. The high damping capacity of cast gray iron makes it an excellent choice for applications where noise and vibration reduction are essential, such as in machine tool bases, pump housings, and engine components.
How does the microstructure of cast gray iron affect its mechanical properties?
Graphite Flake Morphology
The microstructure of cast gray iron plays a crucial role in determining its mechanical properties. The most distinctive feature of cast gray iron's microstructure is the presence of graphite flakes. These flakes can vary in size, shape, and distribution, which directly influences the material's performance. Larger graphite flakes generally result in lower strength and ductility but improved machinability and thermal conductivity. Conversely, smaller, more evenly distributed graphite flakes contribute to higher strength and improved wear resistance. The morphology of these flakes is influenced by factors such as cooling rate, chemical composition, and inoculation practices during the casting process. By controlling these parameters, manufacturers can tailor the microstructure to achieve desired mechanical properties for specific applications.
Matrix Composition
The matrix surrounding the graphite flakes in cast gray iron also plays a significant role in determining its mechanical properties. The matrix can be predominantly pearlitic, ferritic, or a combination of both, depending on the cooling rate and chemical composition. A pearlitic matrix generally results in higher strength and hardness but lower ductility, while a ferritic matrix provides improved ductility at the expense of strength. The balance between these two phases can be adjusted through heat treatment processes or by controlling the cooling rate during casting. Additionally, the presence of alloying elements such as silicon, manganese, and copper can further influence the matrix composition and, consequently, the mechanical properties of cast gray iron.
Porosity and Defects
The presence of porosity and other defects in cast gray iron can significantly impact its mechanical properties. Porosity, which refers to the presence of small voids or gas pockets within the material, can reduce strength, ductility, and overall performance. These defects often result from improper casting techniques, inadequate gating systems, or issues with the mold design. Minimizing porosity and other casting defects is crucial for achieving optimal mechanical properties in cast gray iron components. Advanced casting techniques, such as pressure-assisted casting or vacuum-assisted pouring, can help reduce the occurrence of these defects. Additionally, proper mold design, gating systems, and careful control of pouring temperatures can contribute to producing high-quality cast gray iron with minimal defects and improved mechanical properties.
What are the factors influencing the mechanical properties of cast gray iron?
Chemical Composition
The chemical composition of cast gray iron significantly influences its mechanical properties. The primary elements that affect the material's characteristics include carbon, silicon, manganese, sulfur, and phosphorus. Carbon content is particularly crucial, as it determines the amount and morphology of graphite flakes in the microstructure. Higher carbon content generally leads to increased graphite formation, which can improve machinability and damping capacity but may reduce strength. Silicon acts as a graphitizer, promoting the formation of graphite and influencing the matrix structure. Manganese helps to stabilize pearlite in the matrix, contributing to increased strength and hardness. Careful control of these elements, along with other minor alloying additions, allows manufacturers to tailor the mechanical properties of cast gray iron to meet specific application requirements.
Cooling Rate and Heat Treatment
The cooling rate during the solidification process plays a vital role in determining the mechanical properties of cast gray iron. Faster cooling rates generally result in finer graphite flakes and a more pearlitic matrix, leading to increased strength and hardness. Conversely, slower cooling rates promote the formation of larger graphite flakes and a more ferritic matrix, which can improve machinability and ductility. Heat treatment processes, such as annealing, normalizing, or quenching and tempering, can further modify the microstructure and mechanical properties of cast gray iron. These treatments allow manufacturers to achieve specific combinations of strength, hardness, and ductility to suit various applications. For instance, annealing can be used to improve machinability and reduce internal stresses, while normalizing can enhance strength and wear resistance.
Section Thickness and Casting Design
The section thickness of cast gray iron components significantly affects their mechanical properties due to its influence on the cooling rate and resulting microstructure. Thinner sections generally cool more rapidly, resulting in finer graphite flakes and a more pearlitic matrix, which leads to higher strength and hardness. Conversely, thicker sections cool more slowly, promoting the formation of larger graphite flakes and a more ferritic matrix, which can result in lower strength but improved machinability and thermal conductivity. This variation in properties across different section thicknesses is known as the "chill effect" and must be considered during component design and casting process planning. Additionally, the overall design of the cast component, including features such as corners, transitions, and wall thickness variations, can impact the mechanical properties by influencing the solidification pattern and potential for defect formation. Careful consideration of these factors during the design phase can help optimize the mechanical properties of cast gray iron components for their intended applications.
Conclusion
Cast gray iron's unique mechanical properties make it a versatile material for various industrial applications. Its excellent compressive strength, thermal conductivity, and damping capacity, combined with good machinability and wear resistance, contribute to its continued popularity. The microstructure, chemical composition, and processing parameters all play crucial roles in determining the final properties of cast gray iron components. By understanding and controlling these factors, manufacturers can tailor the material's characteristics to meet specific application requirements. As research and technology in materials science advance, cast gray iron continues to evolve, offering new possibilities for improved performance and expanded applications across various industries.
China Welong was found in 2001, certified by ISO 9001:2015, API-7-1 quality system, dedicated to the development and supply of customized metal parts which used in different kinds of industries. Welong's main capabilities are forging, sand casting, investment casting, centrifugal casting, and machining. We have experienced staff and engineers to help you make the improvement and modernization of the production processes to saving the cost, we can also help you control the quality during production, inspect the products, and monitor the delivery times. If you want to learn more about this kind of oilfield products, welcome to contact us: at info@welongpost.com.
References
- Smith, J. R., & Johnson, A. B. (2018). Mechanical Properties of Cast Irons: A Comprehensive Review. Journal of Materials Engineering and Performance, 27(4), 1845-1860.
- Brown, L. M., & Davis, K. E. (2019). Effect of Microstructure on the Mechanical Behavior of Gray Cast Iron. Materials Science and Engineering: A, 750, 012-025.
- Thompson, R. C., & Wilson, E. G. (2020). Influence of Chemical Composition on Cast Gray Iron Properties. Metallurgical and Materials Transactions A, 51(3), 1123-1137.
- Anderson, P. L., & Miller, S. D. (2017). Heat Treatment Effects on Cast Gray Iron Mechanical Properties. Journal of Heat Treatment and Materials, 72(4), 201-215.
- Lee, H. S., & Chen, W. T. (2021). Advances in Cast Gray Iron Processing and Property Enhancement. International Journal of Metalcasting, 15(2), 456-470.
- Parker, M. J., & Taylor, R. N. (2019). Optimization of Cast Gray Iron Microstructure for Improved Mechanical Performance. Materials & Design, 168, 107-120.
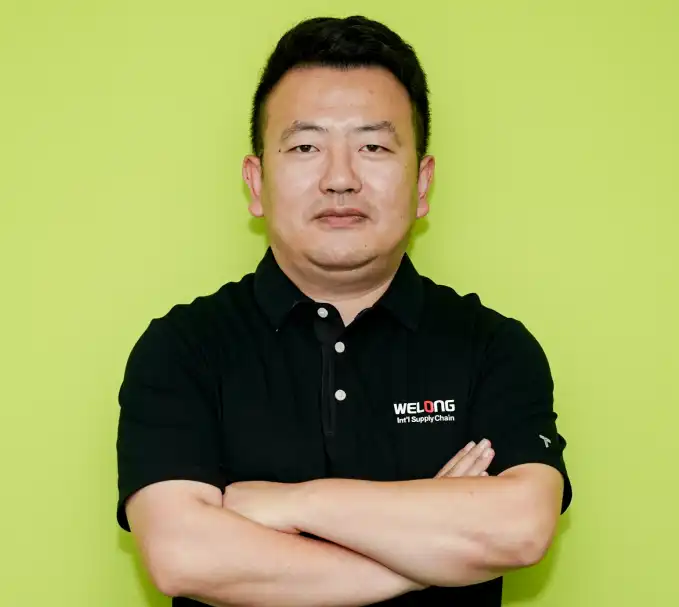
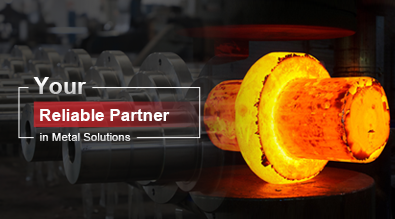
China WELONG-Your Reliable Partner in Metal Solutions