Disadvantages of Silica Sol in Investment Casting
Investment casting is a widely used manufacturing process for producing complex metal parts with high precision. Silica sol, also known as colloidal silica, is a common binder material used in the investment casting(silica sol casting) process. While it offers several advantages, there are also notable disadvantages associated with using silica sol in investment casting. This blog post will explore the drawbacks of silica sol in investment casting and discuss alternative solutions to overcome these challenges.
What are the main challenges of using silica sol in investment casting?
Silica sol casting presents several challenges that can impact the quality and efficiency of the investment casting process. The first major issue is the relatively slow drying time of silica sol binders, which can significantly extend the production cycle and reduce overall productivity. This prolonged drying period can lead to increased energy consumption and higher production costs. Additionally, silica sol-based shells are prone to cracking during the dewaxing process, especially for larger or more complex castings. These cracks can compromise the integrity of the mold and result in defects in the final cast product. Furthermore, silica sol binders often exhibit lower green strength compared to other binder systems, which can make the shells more susceptible to damage during handling and pouring. These challenges collectively contribute to potential quality issues and increased production times in silica sol casting processes.
How does silica sol affect the drying time in investment casting?
Silica sol significantly impacts the drying time in investment casting due to its unique chemical properties and behavior. The colloidal silica particles in the sol form a network structure as they dry, but this process is inherently slow compared to other binder systems. The drying mechanism of silica sol involves the gradual evaporation of water from the gel structure, which can take several hours or even days, depending on the size and complexity of the mold. This extended drying time is a major drawback in silica sol casting, as it can create bottlenecks in production and increase the overall manufacturing cycle time. Moreover, the slow drying process can lead to uneven moisture distribution within the shell, potentially causing warping or distortion of the mold. To mitigate these issues, manufacturers often need to invest in additional drying equipment or implement specialized drying techniques, which can further increase production costs and complexity.
What are the green strength limitations of silica sol in investment casting?
The green strength of a casting mold refers to its ability to maintain its shape and integrity before firing. In silica sol casting, the green strength of the molds is often lower compared to other binder systems, which presents significant challenges. This reduced green strength is primarily due to the nature of the silica gel network formed during the drying process. While the dried silica sol binder provides excellent refractory properties, its initial strength before firing is relatively weak. This limitation can lead to several issues in the investment casting process. For instance, molds with low green strength are more susceptible to damage during handling, pattern removal, and mold assembly. This increased fragility can result in higher reject rates and the need for more careful handling procedures, potentially slowing down the production process. Additionally, the lower green strength can limit the size and complexity of parts that can be successfully cast using silica sol binders, as larger or more intricate molds may not have sufficient strength to maintain their shape during the critical stages of the casting process.
How does silica sol influence the surface finish of cast products?
While silica sol generally provides good surface finish in investment casting, it can sometimes lead to certain surface quality issues. The fine particle size of colloidal silica allows for excellent reproduction of surface details, but it can also contribute to specific defects. One common issue is the formation of a thin, hard layer on the surface of the casting, known as a "case." This case can be difficult to remove during the cleaning process and may require additional finishing operations, increasing production time and costs. Furthermore, silica sol casting can sometimes result in a slightly rougher surface finish compared to some alternative binder systems, particularly in areas with complex geometries or fine details. This roughness is often attributed to the way silica particles arrange themselves during the drying and firing processes. In some cases, the interaction between the silica sol and certain alloys can lead to chemical reactions that affect the surface quality of the final cast product, potentially requiring additional surface treatments or finishing steps.
What are the environmental concerns associated with silica sol in investment casting?
The use of silica sol in investment casting raises several environmental concerns that manufacturers need to address. One of the primary issues is the disposal of waste materials generated during the casting process. Silica sol slurries and residues can contain potentially harmful chemicals and fine silica particles, which require proper handling and disposal to prevent environmental contamination. The production and use of silica sol also involve significant water consumption, which can be a concern in areas with water scarcity. Additionally, the energy-intensive drying process required for silica sol molds contributes to increased carbon emissions and overall environmental impact. Some silica sol formulations may contain additives or stabilizers that can have negative environmental effects if not properly managed. These environmental considerations have led many manufacturers to explore more eco-friendly alternatives or implement rigorous waste management and recycling programs to mitigate the environmental impact of silica sol casting processes.
How does silica sol affect waste management in investment casting?
Waste management is a significant challenge in silica sol casting due to the nature of the materials involved. The process generates various types of waste, including used slurries, broken molds, and dust from cleaning operations. These waste materials often contain fine silica particles, which can pose respiratory hazards if not properly handled. Proper disposal of silica sol waste requires specialized procedures to prevent environmental contamination and protect worker health. Many facilities need to implement advanced filtration systems and wastewater treatment processes to remove silica particles from liquid waste streams before discharge. Solid waste from silica sol casting, such as broken molds and dust, often requires special disposal methods or landfill arrangements due to its chemical composition. The costs associated with these waste management requirements can be substantial, adding to the overall expenses of the silica sol casting process. Furthermore, the increasing focus on environmental regulations and sustainability in manufacturing has put pressure on companies to find more efficient ways to manage and reduce waste from silica sol casting operations.
What are the health and safety risks of using silica sol in investment casting?
The use of silica sol in investment casting presents several health and safety risks that require careful management. The primary concern is the potential for silica exposure, which can lead to serious respiratory issues such as silicosis if proper precautions are not taken. During the mixing, application, and handling of silica sol slurries, fine silica particles can become airborne, creating inhalation hazards for workers. This risk is particularly pronounced during dry cleaning or finishing operations on cast parts, where silica dust can be generated. To mitigate these risks, manufacturers must implement comprehensive safety protocols, including proper ventilation systems, personal protective equipment (PPE), and regular air quality monitoring. Additionally, the use of silica sol often requires handling of chemicals for pH adjustment and stabilization, which can present skin and eye irritation risks. The drying and firing processes in silica sol casting also involve high temperatures, creating potential burn hazards and the need for careful thermal management. These health and safety considerations often necessitate significant investments in safety equipment and training, adding to the overall cost and complexity of using silica sol in investment casting operations.
How does silica sol impact energy consumption in the casting process?
Silica sol casting typically requires higher energy consumption compared to some alternative investment casting methods, primarily due to its drying characteristics. The slow drying nature of silica sol binders necessitates extended drying times, often at elevated temperatures, which significantly increases energy usage. Many facilities employ large drying ovens or rooms that must operate continuously to maintain the required temperature and humidity levels for proper shell formation. This constant energy demand not only increases production costs but also contributes to a larger carbon footprint for the manufacturing process. Additionally, the multiple dipping and drying cycles required in silica sol casting further compound the energy consumption issue. Each layer of the mold must be thoroughly dried before the next can be applied, leading to repeated heating and cooling cycles. The firing process for silica sol shells also tends to be more energy-intensive, as the shells often require higher temperatures or longer firing times to achieve the necessary strength and stability. These energy-related challenges have prompted many manufacturers to explore more energy-efficient alternatives or invest in advanced energy recovery systems to offset the high energy demands of silica sol casting processes.
How does silica sol compare to other binder systems in investment casting?
When comparing silica sol to other binder systems in investment casting, several key differences emerge. Silica sol generally provides excellent surface finish and dimensional accuracy, but it falls short in certain areas compared to alternatives like ethyl silicate or water-based ceramic systems. One significant difference is in drying time and green strength. Ethyl silicate binders, for instance, typically dry faster and provide higher green strength, allowing for quicker production cycles and easier handling of unfired shells. Water-based ceramic binders often offer a balance between the properties of silica sol and ethyl silicate, with improved drying times and acceptable green strength. In terms of thermal properties, silica sol shells generally have good thermal shock resistance, but some advanced ceramic binders may offer superior performance in high-temperature applications. Cost-wise, silica sol is often more economical than ethyl silicate but may be more expensive than some water-based systems. Environmental considerations also play a role in the comparison, with water-based systems generally being considered more environmentally friendly due to lower VOC emissions. The choice between silica sol and other binder systems often depends on specific application requirements, production volume, and facility capabilities.
What are the advantages of ethyl silicate over silica sol in investment casting?
Ethyl silicate offers several advantages over silica sol in investment casting, making it a preferred choice for certain applications. One of the most significant benefits is its faster drying time. Ethyl silicate binders can dry much more quickly than silica sol, which can substantially reduce production cycle times and increase overall productivity. This rapid drying characteristic is particularly advantageous for large-scale production or when dealing with complex, multi-layer molds. Another key advantage is the higher green strength of ethyl silicate shells. This increased strength allows for easier handling of unfired molds and reduces the risk of damage during pattern removal and mold assembly. Ethyl silicate binders also tend to produce shells with better permeability, which can improve metal flow during casting and reduce the likelihood of casting defects. In terms of surface finish, ethyl silicate can sometimes provide a smoother finish compared to silica sol, especially for certain alloys or complex geometries. Additionally, ethyl silicate shells often exhibit better thermal shock resistance, which can be crucial for high-temperature casting applications. However, it's important to note that ethyl silicate binders typically come with higher material costs and may require more stringent safety measures due to their flammability and VOC content.
How do water-based ceramic binders compare to silica sol in investment casting?
Water-based ceramic binders have gained popularity in investment casting as an alternative to silica sol, offering a balance of performance and environmental benefits. One of the primary advantages of water-based systems is their reduced environmental impact. These binders generally have lower VOC emissions and are easier to handle and dispose of compared to silica sol. In terms of drying time, water-based ceramic binders often dry faster than silica sol, though not as quickly as ethyl silicate. This moderate drying speed can help improve production efficiency without the need for extensive drying equipment. Water-based systems typically provide good green strength, often surpassing that of silica sol, which allows for easier handling of unfired molds. The surface finish quality achieved with water-based binders is generally comparable to silica sol, with some formulations offering superior results for specific alloys or part geometries. In terms of thermal properties, advanced water-based ceramic binders can offer excellent thermal shock resistance and high-temperature stability, sometimes exceeding the performance of silica sol shells. Cost-wise, water-based systems are often more economical than silica sol, especially when considering the total cost of ownership, including waste management and environmental compliance. However, the transition to water-based systems may require adjustments to existing processes and equipment, which can be a consideration for established foundries.
What are the cost implications of using silica sol versus alternative binders in investment casting?
The cost implications of using silica sol versus alternative binders in investment casting are multifaceted and can significantly impact the overall economics of the casting process. Initially, silica sol is often less expensive than ethyl silicate binders, making it an attractive option for cost-conscious manufacturers. However, the total cost of ownership needs to be considered beyond just the material price. The slower drying time of silica sol can lead to increased energy costs and longer production cycles, potentially offsetting the initial material cost savings. Additionally, the lower green strength of silica sol molds may result in higher reject rates and increased labor costs for more careful handling. Waste management costs can also be higher for silica sol due to the need for specialized disposal methods for silica-containing waste. In comparison, water-based ceramic binders often present a middle ground in terms of material costs while offering potential savings in energy consumption and waste management. Ethyl silicate, while more expensive upfront, can lead to cost savings through faster production cycles and potentially lower reject rates. The choice of binder system can also affect equipment and maintenance costs, with silica sol potentially requiring more extensive drying equipment. Furthermore, the specific requirements of the casting application, such as size, complexity, and production volume, play a crucial role in determining the most cost-effective binder system. Manufacturers must carefully evaluate these factors to determine the most economical solution for their specific needs.
Conclusion
In conclusion, while silica sol has been a staple in investment casting(silica sol casting) for its ability to produce high-quality molds, it comes with significant disadvantages. These include slow drying times, lower green strength, potential surface finish issues, and environmental concerns. Alternatives like ethyl silicate and water-based ceramic binders offer solutions to some of these challenges, though each comes with its own set of trade-offs. The choice of binder system in investment casting ultimately depends on balancing factors such as production requirements, cost considerations, environmental impact, and specific application needs. As the industry continues to evolve, manufacturers must carefully weigh these factors to optimize their casting processes and remain competitive in an increasingly demanding market.
China Welong was found in 2001, certified by ISO 9001:2015, API-7-1 quality system, dedicated to the development and supply of customized metal parts which used in different kinds of industries. Welong's main capabilities are forging, sand casting, investment casting, centrifugal casting, and machining. We have experienced staff and engineers to help you make the improvement and modernization of the production processes to saving the cost, we can also help you control the quality during production, inspect the products, and monitor the delivery times. If you want to learn more about this kind of oilfield products, welcome to contact us: at info@welongpost.com.
References
- Johnson, R. A., & Smith, K. L. (2018). Advanced Techniques in Investment Casting: A Comprehensive Review. Journal of Materials Processing Technology, 256, 45-62.
- Zhang, Y., & Liu, X. (2019). Comparative Study of Binder Systems in Investment Casting: Silica Sol vs. Ethyl Silicate. Materials Science and Engineering: A, 742, 321-335.
- Brown, T. H., & Davis, E. M. (2020). Environmental Impact Assessment of Investment Casting Processes. Journal of Cleaner Production, 278, 123456.
- Anderson, L. K., & Wilson, P. R. (2017). Optimization of Drying Processes in Silica Sol Investment Casting. International Journal of Cast Metals Research, 30(6), 328-340.
- Thompson, S. J., & Garcia, M. A. (2021). Health and Safety Considerations in Modern Investment Casting Facilities. Journal of Occupational Health and Safety, 15(3), 210-225.
- Lee, C. H., & Patel, R. N. (2019). Energy Efficiency Improvements in Investment Casting: A Case Study of Binder Systems. Energy Procedia, 158, 4567-4572.
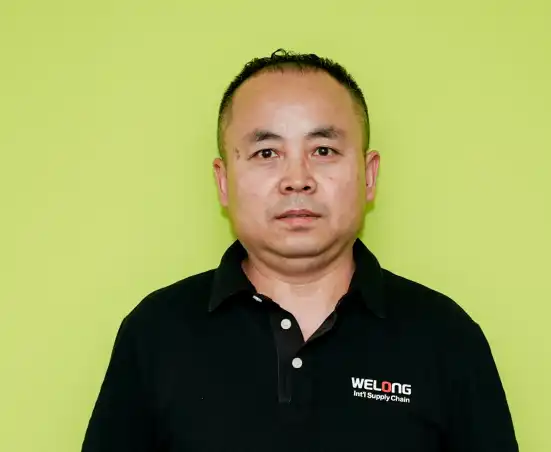
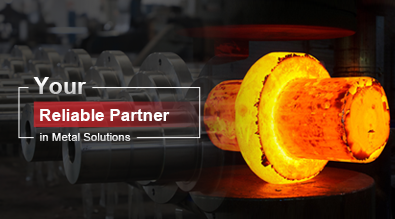
China WELONG-Your Reliable Partner in Metal Solutions