How Do Furnace Rolls Influence the Cooling Process in Heat Treatment?
Furnace rolls play a crucial role in the cooling process during heat treatment, significantly impacting the final quality and properties of materials. These cylindrical components, typically made from heat-resistant alloys, are essential in controlled cooling applications within industrial furnaces. Furnace rolls influence the cooling process by facilitating uniform heat distribution, controlling cooling rates, and maintaining precise temperature gradients. Their design, material composition, and operational parameters directly affect the cooling efficiency and consistency across the treated materials. By providing a stable and adjustable platform for materials to cool, furnace rolls enable manufacturers to achieve desired microstructures, mechanical properties, and overall product quality. The strategic placement and rotation of these rolls ensure even cooling, preventing issues like warping or uneven hardening that can occur during rapid or uncontrolled cooling. Understanding the intricate relationship between furnace rolls and the cooling process is vital for optimizing heat treatment operations across various industries, from metallurgy to advanced materials processing.
The Role of Furnace Rolls in Heat Treatment Processes
Material Composition and Properties of Furnace Rolls
Furnace rolls are typically manufactured using high-temperature resistant alloys such as heat-resistant stainless steel, nickel-based superalloys, or ceramic composites. These materials are chosen for their ability to withstand extreme temperatures, resist thermal fatigue, and maintain dimensional stability under cyclic heating and cooling conditions. The specific alloy composition can be tailored to suit different heat treatment processes and environmental requirements.
Design Features for Optimal Heat Transfer
The design of furnace rolls incorporates features that enhance heat transfer and promote uniform cooling. These may include internal cooling channels, surface textures to increase contact area, and specialized coatings to improve thermal conductivity or resist oxidation. The diameter, length, and wall thickness of the rolls are carefully engineered to balance thermal mass with heat transfer efficiency.
Integration with Furnace Systems
Furnace rolls are integrated into the overall furnace system through sophisticated support structures and drive mechanisms. This integration allows for precise control of roll rotation speed, positioning, and alignment. Advanced furnace designs may incorporate automated roll changing systems to minimize downtime and ensure consistent performance across long production runs.
Mechanisms of Cooling Influenced by Furnace Rolls
Conductive Heat Transfer
One of the primary mechanisms by which furnace rolls influence cooling is through conductive heat transfer. As heated materials come into contact with the roll surface, heat is conducted from the material to the roll. The rate of conduction depends on factors such as the thermal conductivity of the roll material, the temperature difference between the material and the roll, and the contact area. Rolls with higher thermal conductivity can facilitate more rapid cooling, while those with lower conductivity can be used for more gradual cooling processes.
Convective Cooling Effects
Furnace rolls contribute to convective cooling by facilitating the movement of cooling gases or liquids around the treated materials. The rotation of the rolls can create turbulence in the surrounding atmosphere, enhancing heat transfer from the material surface to the cooler environment. In some cases, rolls may be designed with internal cooling channels through which coolant can be circulated, allowing for more precise control over the cooling rate.
Radiative Heat Dissipation
Radiative heat transfer also plays a role in the cooling process influenced by furnace rolls. The surface properties of the rolls, such as emissivity and reflectivity, affect how heat is radiated from the treated materials. Rolls with high emissivity can absorb more radiant heat from the materials, while those with reflective surfaces can help redirect heat back to the materials, slowing the cooling process when desired.
Optimizing Cooling Processes with Advanced Furnace Roll Technologies
Smart Sensing and Control Systems
Modern furnace roll systems are increasingly equipped with advanced sensing and control technologies. These include embedded thermocouples, infrared cameras, and real-time monitoring systems that provide continuous feedback on temperature distributions and cooling rates. By integrating these sensors with adaptive control algorithms, manufacturers can achieve unprecedented levels of precision in managing the cooling process, adjusting roll speeds, positions, and cooling parameters in real-time to maintain optimal conditions.
Customized Surface Treatments and Coatings
Innovative surface treatments and coatings are being developed to enhance the performance of furnace rolls in cooling applications. These may include ceramic thermal barrier coatings to improve insulation properties, nanostructured surfaces to increase heat transfer efficiency, or self-cleaning coatings to prevent material buildup and ensure consistent performance over extended periods. Such advancements allow for more tailored cooling profiles and improved product quality across a wide range of heat treatment applications.
Hybrid Cooling Strategies
Emerging technologies are exploring hybrid cooling strategies that combine the benefits of furnace rolls with other cooling methods. For example, some systems integrate roll cooling with controlled atmosphere cooling or quenching techniques. These hybrid approaches offer greater flexibility in managing cooling rates and can be particularly beneficial for materials requiring complex heat treatment profiles or for processes where rapid cooling is followed by controlled slow cooling phases.
In conclusion, furnace rolls are indispensable components in modern heat treatment processes, playing a pivotal role in controlling and optimizing the cooling phase. Their influence extends beyond mere material handling, significantly impacting the microstructure, mechanical properties, and overall quality of treated materials. As industries continue to demand higher precision and efficiency in heat treatment operations, the development of advanced furnace roll technologies remains a key area of innovation. For manufacturers seeking to enhance their heat treatment capabilities and achieve superior product quality, understanding and leveraging the full potential of furnace rolls in the cooling process is essential. If you're looking to optimize your heat treatment processes or require custom furnace roll solutions, we invite you to reach out to our team of experts at info@welongpost.com for personalized guidance and support.
References
- Continuous Annealing Furnace Rolls - EB Castworld. (2024, December 9). EB Castworld.
- 5 Experts on Advantages and Applications of Roller Hearth Systems. (2025, January 17). Heat Treat Today.
- Roll Cooling: Understand the Three Heat-Transfer Processes. (2025, January 21). Plastics Technology.
- Roll | Product & Technology | Hyundai Steel - 현대제철. (2024, December 26). Hyundai Steel.
- Radiant Tubes & Furnace Rolls - Ferralloy Inc. (2023, November 8). Ferralloy Inc.
- The Function And Use Of Furnace Roll. (2023, December 27). Refiner Mills.

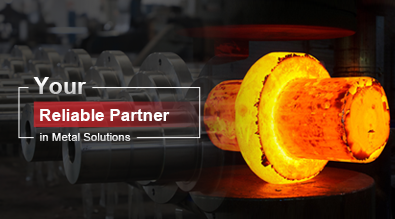
China WELONG-Your Reliable Partner in Metal Solutions