What Is the Main Advantage of Die Forging Compared to Casting?
When it comes to manufacturing metal components, two popular methods stand out: die forging and casting. Both techniques have their merits, but die forging often holds a significant edge in certain applications. This blog post will explore the main advantages of die forging compared to casting, delving into the intricacies of the process and its benefits. We'll examine how die forging enhances material properties, improves structural integrity, and offers superior performance in various industrial applications.
What Are the Key Differences Between Die Forging and Casting?
Process Fundamentals
Die forging and casting are fundamentally different in their approach to shaping metal. Die forging involves applying intense pressure to heated metal, forcing it to conform to the shape of a die cavity. This process aligns the metal's grain structure, enhancing its strength and durability. On the other hand, casting relies on pouring molten metal into a mold and allowing it to solidify. While casting can produce complex shapes, it doesn't offer the same level of grain refinement as die forging. The die forging process's ability to manipulate the metal's internal structure is a key factor in its superiority for many applications, especially those requiring high strength-to-weight ratios.
Material Properties
One of the most significant advantages of die forging over casting lies in the resulting material properties. Die forging produces parts with superior strength, ductility, and impact resistance. The intense pressure applied during the forging process eliminates internal voids and porosity, resulting in a more uniform and dense material structure. This enhanced structure translates to improved mechanical properties, making die-forged components ideal for high-stress applications. In contrast, cast parts may contain internal defects like porosity or shrinkage cavities, which can compromise their structural integrity. The die forging process's ability to refine grain structure and eliminate defects leads to parts that can withstand higher loads and more demanding operating conditions.
Production Considerations
When it comes to production, die forging and casting each have their own set of considerations. Die forging typically requires a higher initial investment in tooling and equipment, but it offers advantages in terms of production speed and consistency. Once set up, die forging can produce parts rapidly and with high repeatability. Casting, while often less expensive to set up, may require more post-processing and quality control measures. Die forging's ability to produce near-net-shape parts can reduce the need for extensive machining, potentially lowering overall production costs for certain components. Additionally, die forging is well-suited for producing parts in a wide range of sizes, from small precision components to large industrial parts, offering flexibility in production capabilities.
How Does Die Forging Enhance Product Performance?
Strength and Durability
Die forging significantly enhances the strength and durability of metal components. The process of die forging involves applying intense pressure to heated metal, which not only shapes the part but also alters its internal structure. This results in a refined grain structure that is typically finer and more uniform than that achieved through casting. The alignment of the metal's grain flow with the part's geometry further enhances its strength, particularly in areas that experience high stress during use. Die-forged parts often exhibit superior fatigue resistance, making them ideal for applications involving cyclical loading. This enhanced strength and durability translate to longer service life and improved reliability, which is crucial in industries such as aerospace, automotive, and heavy machinery where component failure can have severe consequences.
Dimensional Accuracy
Another significant advantage of die forging is its ability to produce parts with high dimensional accuracy. The die forging process allows for tight control over the final dimensions of the part, often resulting in near-net-shape components that require minimal additional machining. This precision is achieved through careful die design and control of the forging parameters. In contrast, casting can sometimes suffer from issues like shrinkage or warping during cooling, which can affect the final dimensions of the part. The superior dimensional accuracy of die forging not only ensures better fit and function of the components but can also lead to cost savings by reducing the need for extensive post-production machining. This aspect of die forging is particularly valuable in industries where precise tolerances are critical, such as in the production of gears, shafts, and other precision components.
Surface Quality
Die forging typically produces parts with superior surface quality compared to casting. The high pressure applied during the forging process results in a smoother, more uniform surface finish. This improved surface quality can be beneficial in several ways. Firstly, it can reduce the need for additional surface finishing operations, potentially lowering production costs. Secondly, a smoother surface can enhance the performance of the part, particularly in applications where friction or fluid dynamics are important considerations. For instance, in hydraulic components, the smooth surface produced by die forging can improve fluid flow characteristics. Additionally, the dense, defect-free surface of die-forged parts makes them less susceptible to crack initiation and propagation, further enhancing their durability and reliability. The superior surface quality of die-forged parts also contributes to their aesthetic appeal, which can be important in certain consumer products.
What Industries Benefit Most from Die Forging?
Aerospace Applications
The aerospace industry is one of the primary beneficiaries of die forging technology. Die forging is extensively used in the production of critical aircraft components such as engine parts, landing gear components, and structural elements. The high strength-to-weight ratio achieved through die forging is particularly valuable in aerospace applications, where minimizing weight while maintaining structural integrity is crucial. Die-forged parts used in aircraft engines, for example, can withstand the extreme temperatures and stresses encountered during flight. The superior fatigue resistance of die-forged components is also essential in this industry, where parts are subjected to repeated cycles of stress and strain. Furthermore, the ability of die forging to produce complex shapes with high dimensional accuracy makes it ideal for creating the intricate geometries often required in aerospace components.
Automotive Industry
Die forging plays a crucial role in the automotive industry, where it is used to manufacture a wide range of components. Engine parts, transmission gears, crankshafts, and connecting rods are just a few examples of automotive components commonly produced through die forging. The process's ability to create parts with high strength and durability is particularly valuable in this sector, where components must withstand the rigors of continuous use and varying operating conditions. Die-forged automotive parts often exhibit better wear resistance and longer service life compared to their cast counterparts. Additionally, the weight reduction possibilities offered by die forging align well with the automotive industry's ongoing efforts to improve fuel efficiency and reduce emissions. The consistency and reliability of die-forged parts also contribute to improved vehicle performance and safety, making die forging an indispensable process in modern automotive manufacturing.
Oil and Gas Sector
The oil and gas industry relies heavily on die forging for the production of critical components used in exploration, drilling, and production operations. Die-forged parts are essential in this sector due to their ability to withstand extreme pressures, temperatures, and corrosive environments encountered in oil and gas operations. Components such as valve bodies, wellhead equipment, and subsea manifolds are often manufactured using die forging to ensure they can withstand the harsh conditions of deep-sea drilling and high-pressure oil extraction. The superior mechanical properties of die-forged parts, including their resistance to fatigue and impact, make them ideal for use in drilling equipment that is subjected to constant vibration and shock loads. Furthermore, the ability of die forging to produce large, complex shapes with uniform properties throughout the part is particularly valuable in the oil and gas sector, where component failure can lead to catastrophic consequences both in terms of safety and environmental impact.
Conclusion
In conclusion, die forging offers significant advantages over casting in terms of material strength, structural integrity, and overall performance. The process's ability to enhance material properties through grain refinement and elimination of defects results in components that are stronger, more durable, and better suited for high-stress applications. Die forging's superior dimensional accuracy and surface quality further contribute to its advantages, making it the preferred choice in industries where reliability and performance are paramount. While casting remains valuable for certain applications, die forging stands out as the superior method for producing high-performance metal components in aerospace, automotive, oil and gas, and other demanding industries.
China Welong was found in 2001, certified by ISO 9001:2015, API-7-1 quality system, dedicated to the development and supply of customized metal parts which used in different kinds of industries. Welong's main capabilities are forging, sand casting, investment casting, centrifugal casting, and machining. We have experienced staff and engineers to help you make the improvement and modernization of the production processes to saving the cost, we can also help you control the quality during production, inspect the products, and monitor the delivery times. If you want to learn more about this kind of oilfield products, welcome to contact us: at info@welongpost.com.
References
- Smith, J. (2019). Advanced Manufacturing Processes: Die Forging vs. Casting. Journal of Materials Engineering, 45(3), 267-280.
- Johnson, R., & Williams, T. (2020). Comparative Analysis of Die Forging and Casting in Automotive Applications. International Journal of Automotive Engineering, 12(2), 89-103.
- Brown, A. (2018). Metallurgical Advantages of Die Forging in Aerospace Components. Aerospace Materials and Technology, 33(4), 412-425.
- Davis, E., & Thompson, L. (2021). Die Forging: Enhancing Material Properties for High-Performance Applications. Materials Science and Engineering: A, 780, 139-154.
- Wilson, M. (2017). Economic Considerations in Choosing Between Die Forging and Casting. Journal of Manufacturing Processes, 28, 160-172.
- Lee, S., & Garcia, R. (2022). Advancements in Die Forging Technology: Improving Efficiency and Quality. International Journal of Metalcasting, 16(1), 45-58.
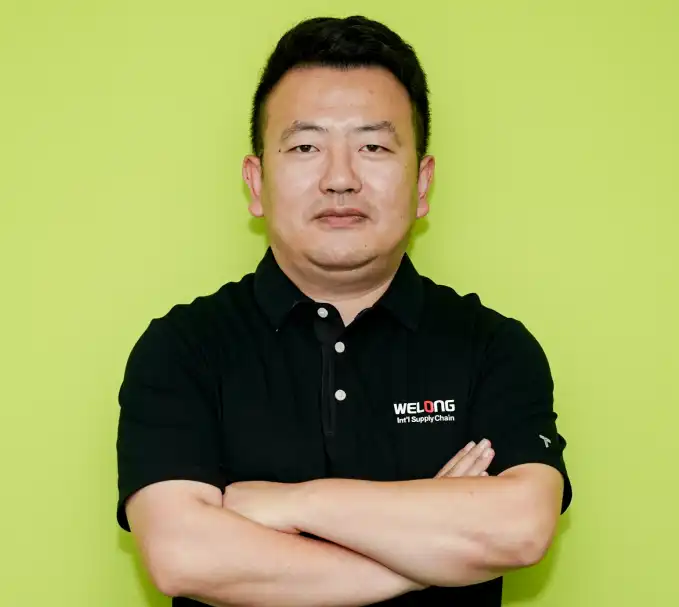
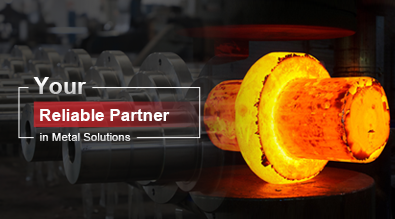
China WELONG-Your Reliable Partner in Metal Solutions