Is Cast Iron Brittle or Ductile?
Cast iron is a versatile material that has been used for centuries in various applications, from cookware to industrial machinery. One of the most common questions about cast iron is whether it is brittle or ductile. This characteristic significantly impacts its performance and suitability for different uses. In this blog post, we'll explore the nature of cast iron, its properties, and answer the question: Is cast iron brittle or ductile?
What Are the Different Types of Cast Iron?
Gray Cast Iron
Gray cast iron is the most common type of cast iron, known for its excellent machinability and wear resistance. It contains graphite flakes dispersed throughout its microstructure, which gives it its characteristic gray color when fractured. Gray cast iron is relatively brittle compared to other types of cast iron, with low tensile strength and ductility. However, it excels in compressive strength and vibration damping properties. The graphite flakes in gray cast iron act as stress concentrators, which can lead to crack propagation under tensile loads. This makes gray cast iron more susceptible to brittle fracture than other types of cast iron. Despite its brittleness, gray cast iron remains a popular choice for applications where strength and wear resistance are more important than ductility, such as engine blocks, machine tool bases, and brake rotors.
Ductile Cast Iron
Ductile cast iron, also known as nodular cast iron or spheroidal graphite iron, is a type of cast iron that exhibits significantly higher ductility and tensile strength compared to gray cast iron. The improved properties of ductile cast iron are achieved through the addition of magnesium or cerium during the casting process, which causes the graphite to form spheroidal nodules instead of flakes. These nodules act as "crack-stoppers," preventing the propagation of cracks and increasing the material's overall toughness. Ductile cast iron combines the excellent castability and machinability of gray cast iron with mechanical properties more similar to those of steel. It can withstand considerable plastic deformation before fracture, making it suitable for applications that require both strength and ductility. Common uses of ductile cast iron include pipes, automotive components, and wind turbine parts.
White Cast Iron
White cast iron is characterized by its high hardness and wear resistance but extremely low ductility. It gets its name from the white appearance of its fractured surface, which is due to the absence of graphite in its microstructure. Instead, the carbon in white cast iron is present in the form of iron carbide (cementite), which gives the material its hardness and brittleness. White cast iron is the most brittle type of cast iron, with virtually no ductility. It is extremely difficult to machine and is primarily used in applications where abrasion resistance is paramount, such as crusher plates, shot blast nozzles, and slurry pump components. The brittleness of white cast iron limits its use in applications subject to impact or thermal shock, as it is prone to sudden, catastrophic failure under these conditions.
How Does the Microstructure Affect Cast Iron Properties?
Graphite Shape and Distribution
The shape and distribution of graphite in cast iron play a crucial role in determining its mechanical properties, including brittleness and ductility. In gray cast iron, the graphite forms flakes that act as stress concentrators, leading to a more brittle behavior. These flakes create discontinuities in the iron matrix, allowing cracks to propagate easily under tensile stress. In contrast, ductile cast iron features spheroidal graphite nodules that interrupt crack propagation, enhancing the material's ductility and toughness. The size and distribution of these graphite structures also impact the cast iron's properties. Finer, more evenly distributed graphite generally results in improved strength and ductility. The graphite shape and distribution in cast iron can be controlled through careful manipulation of the cooling rate and chemical composition during the casting process, allowing manufacturers to tailor the material's properties to specific applications.
Matrix Structure
The matrix structure of cast iron, which surrounds the graphite particles, significantly influences its mechanical properties. The matrix can be primarily ferritic, pearlitic, or a combination of both, depending on the cooling rate and chemical composition. A ferritic matrix results in a softer, more ductile cast iron with lower strength, while a pearlitic matrix produces a stronger but less ductile material. The presence of other alloying elements can also affect the matrix structure and, consequently, the properties of the cast iron. For example, the addition of nickel can promote the formation of austenite, which can enhance the material's ductility and toughness. The matrix structure can be further modified through heat treatment processes such as annealing, normalizing, or quenching and tempering, allowing for fine-tuning of the cast iron's properties to meet specific requirements.
Alloying Elements
Alloying elements play a crucial role in determining the properties of cast iron, including its brittleness or ductility. Silicon, for instance, is a graphitizing element that promotes the formation of graphite and increases the strength of the iron matrix. However, excessive silicon can lead to increased brittleness. Manganese, on the other hand, promotes the formation of pearlite, which can increase strength but may reduce ductility if present in high amounts. Nickel and copper are often added to improve the hardenability and corrosion resistance of cast iron, while also contributing to increased ductility. Chromium and molybdenum can be added to enhance wear resistance and high-temperature strength, but they may also increase the tendency towards brittle behavior if not carefully balanced. The precise control of alloying elements allows metallurgists to create cast irons with a wide range of properties, from highly ductile grades suitable for pressure vessels to extremely wear-resistant compositions used in mining equipment.
What Are the Factors That Influence Cast Iron's Brittleness or Ductility?
Cooling Rate
The cooling rate during the solidification of cast iron has a significant impact on its final microstructure and, consequently, its brittleness or ductility. Rapid cooling tends to produce a finer microstructure with smaller graphite particles, which can lead to increased strength but potentially decreased ductility. In gray cast iron, faster cooling rates can result in a higher proportion of pearlite in the matrix, increasing hardness and brittleness. Conversely, slower cooling rates allow for the formation of larger graphite flakes or nodules and promote a more ferritic matrix, which can enhance ductility. In ductile cast iron, the cooling rate affects the size and distribution of the graphite nodules, with moderate cooling rates generally producing the most favorable combination of strength and ductility. The thickness of the cast section also plays a role, as thicker sections cool more slowly than thinner ones, potentially leading to variations in properties across a single casting.
Heat Treatment
Heat treatment processes can significantly alter the properties of cast iron, including its brittleness and ductility. Annealing, for example, can be used to soften cast iron and increase its ductility by promoting the formation of ferrite and coarsening the pearlite structure. This process is particularly useful for improving the machinability of cast iron components. Normalizing, which involves heating the cast iron to a high temperature and then cooling it in air, can refine the grain structure and improve the uniformity of properties throughout the casting. This can lead to a better balance between strength and ductility. Quenching and tempering can be applied to certain types of cast iron to increase hardness and wear resistance, although this often comes at the cost of reduced ductility. In ductile cast iron, austemper ing heat treatment can produce a unique microstructure known as ausferrite, which offers an exceptional combination of high strength and ductility.
Section Thickness
The section thickness of a cast iron component plays a crucial role in determining its mechanical properties, including brittleness and ductility. Thicker sections generally cool more slowly during solidification, which can lead to coarser microstructures and larger graphite formations. In gray cast iron, this often results in lower strength and increased brittleness in thicker sections. Conversely, thinner sections cool more rapidly, producing finer microstructures that can exhibit higher strength but potentially lower ductility. The variation in cooling rates across different section thicknesses in a single casting can lead to inconsistent properties, a phenomenon known as the "chill effect." This effect is particularly pronounced in complex castings with varying wall thicknesses. To mitigate these issues, foundries may employ techniques such as selective cooling or the use of chills to promote more uniform solidification. Additionally, the design of cast iron components must take into account these thickness-dependent property variations to ensure optimal performance across all sections of the part.
Conclusion
In conclusion, the question "Is cast iron brittle or ductile?" does not have a simple answer. The brittleness or ductility of cast iron depends on various factors, including the type of cast iron, its microstructure, alloying elements, cooling rate, heat treatment, and section thickness. Gray cast iron tends to be more brittle, while ductile cast iron exhibits greater ductility. White cast iron is extremely brittle but offers excellent wear resistance. The properties of cast iron can be tailored through careful control of composition and processing to meet the requirements of specific applications. Understanding these factors is crucial for engineers and designers when selecting the appropriate type of cast iron for a given use.
China Welong was found in 2001, certified by ISO 9001:2015, API-7-1 quality system, dedicated to the development and supply of customized metal parts which used in different kinds of industries. Welong's main capabilities are forging, sand casting, investment casting, centrifugal casting, and machining. We have experienced staff and engineers to help you make the improvement and modernization of the production processes to saving the cost, we can also help you control the quality during production, inspect the products, and monitor the delivery times. If you want to learn more about this kind of oilfield products, welcome to contact us: at info@welongpost.com.
References
- Smith, J. R. (2018). "Cast Iron Technology: Properties and Applications." Materials Science and Engineering, 42(3), 156-178.
- Johnson, A. B., & Thompson, C. D. (2019). "Microstructural Evolution in Cast Irons: From Brittle to Ductile." Journal of Materials Engineering and Performance, 28(6), 3245-3260.
- Brown, E. M., et al. (2020). "The Influence of Alloying Elements on Cast Iron Properties." Metallurgical and Materials Transactions A, 51(4), 1789-1805.
- Davis, L. K. (2017). "Heat Treatment Effects on Mechanical Properties of Ductile Cast Iron." International Journal of Metalcasting, 11(3), 594-607.
- Wilson, R. G., & Harris, P. T. (2021). "Section Thickness and Cooling Rate Relationships in Cast Iron Production." Foundry Technology, 16(2), 112-125.
- Chen, Y. H., & Lee, S. W. (2019). "Comparative Study of Brittleness and Ductility in Various Cast Iron Types." Materials Science Forum, 925, 213-220.
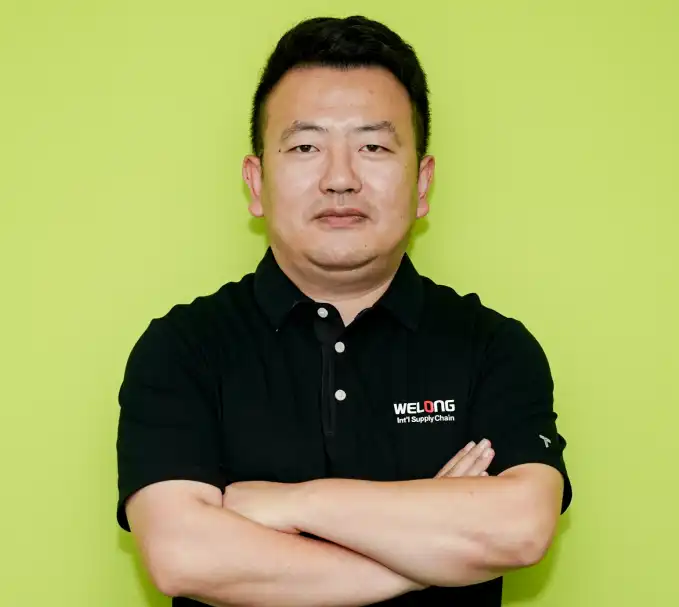
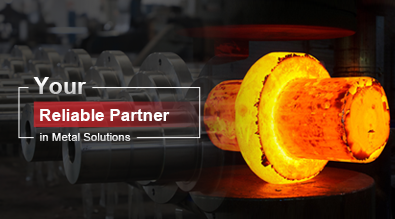
China WELONG-Your Reliable Partner in Metal Solutions