How Do You Make Cast Iron Gray?
Cast gray iron, also known as gray cast iron, is a popular material in various industries due to its excellent properties and versatility. Understanding how to produce this type of iron is crucial for manufacturers and engineers looking to create high-quality components. In this blog post, we'll explore the process of making cast iron gray, discussing key factors, techniques, and considerations that contribute to its production.
What are the key ingredients in producing gray cast iron?
Carbon content and its role
The carbon content in cast gray iron plays a crucial role in determining its properties and appearance. Typically, gray cast iron contains between 2.5% and 4% carbon, which is higher than most steels. This high carbon content contributes to the formation of graphite flakes within the iron matrix, giving it its characteristic gray color and unique properties. The carbon also affects the iron's fluidity during casting, making it easier to pour into complex molds. Manufacturers must carefully control the carbon content to achieve the desired balance between strength, machinability, and thermal conductivity in the final product.
Silicon and its influence
Silicon is another essential element in the production of cast gray iron, typically ranging from 1% to 3% by weight. It acts as a graphitizing agent, promoting the formation of graphite flakes instead of iron carbides. This not only contributes to the gray color but also enhances the iron's castability and machinability. Silicon also helps to increase the fluidity of the molten iron, allowing for better filling of molds and reducing the risk of casting defects. The amount of silicon added must be carefully controlled, as too much can lead to excessive graphite formation, potentially weakening the iron's structure.
Other alloying elements
While carbon and silicon are the primary elements in cast gray iron, other alloying elements can be added to enhance specific properties. Manganese, typically present at 0.5% to 1%, helps to increase strength and hardness. Small amounts of phosphorus (0.05% to 0.2%) can improve fluidity and wear resistance. Sulfur, usually kept below 0.15%, can affect the graphite structure and machinability. Some manufacturers may also add small quantities of elements like chromium, molybdenum, or nickel to further modify the iron's properties. These alloying elements must be carefully balanced to achieve the desired characteristics in the final cast gray iron product.
How does the cooling rate affect gray cast iron production?
Slow cooling and graphite formation
The cooling rate plays a crucial role in the production of cast gray iron, particularly in the formation of graphite flakes. A slow cooling rate is generally preferred for gray cast iron production. This slow cooling allows sufficient time for carbon to precipitate out of the iron solution and form graphite flakes. The size, shape, and distribution of these graphite flakes significantly influence the properties of the final product. Slow cooling promotes the growth of larger, more evenly distributed graphite flakes, which contribute to better machinability, thermal conductivity, and vibration damping properties. Manufacturers must carefully control the cooling rate to ensure the desired microstructure and properties are achieved in the cast gray iron.
Inoculation and its effects
Inoculation is a critical process in the production of cast gray iron, involving the addition of small amounts of certain materials to the molten iron just before casting. Common inoculants include ferrosilicon, calcium-bearing alloys, or rare earth elements. The primary purpose of inoculation is to promote the formation of numerous nucleation sites for graphite growth. This results in a finer, more evenly distributed graphite structure throughout the iron matrix. Inoculation can help control the cooling rate and graphite formation, leading to improved mechanical properties, reduced shrinkage, and better overall quality of the cast gray iron. The type and amount of inoculant used must be carefully selected based on the specific composition and desired properties of the final product.
Section thickness and cooling variations
The thickness of different sections in a cast gray iron component can significantly affect the cooling rate and, consequently, the microstructure and properties of the material. Thicker sections tend to cool more slowly than thinner ones, leading to variations in graphite formation and mechanical properties across the casting. This phenomenon, known as the "chill effect," can result in harder, more wear-resistant surfaces in thin sections and softer, more machinable interiors in thicker areas. To manage these variations, manufacturers must carefully design molds and gating systems, considering factors such as section thickness, pouring temperature, and cooling rate control methods. In some cases, localized cooling or heating techniques may be employed to achieve more uniform properties throughout the cast gray iron component.
What are the key steps in the casting process for gray iron?
Melting and composition control
The first crucial step in the casting process for gray iron is melting and composition control. This typically occurs in a cupola furnace or an electric induction furnace. The raw materials, including pig iron, steel scrap, and various alloying elements, are carefully measured and added to achieve the desired chemical composition. During the melting process, the temperature is closely monitored and controlled to ensure proper carbon dissolution and to prevent excessive oxidation. Manufacturers may perform periodic chemical analysis of the molten iron to make any necessary adjustments to the composition. This precise control of the melt composition is essential for achieving the desired properties in the final cast gray iron product.
Mold preparation and pouring
Mold preparation is a critical step in the production of cast gray iron components. Typically, sand molds are used due to their ability to withstand high temperatures and produce complex shapes. The molds are created using a pattern that represents the desired shape of the final product. The sand mixture, often containing clay and other additives, is compacted around the pattern to form the mold cavity. Once the mold is prepared, the molten gray iron is carefully poured into it. The pouring temperature and rate must be carefully controlled to ensure proper filling of the mold and to minimize defects. Some manufacturers may use automated pouring systems to achieve consistent results across multiple castings.
Solidification and cooling control
After pouring, the cast gray iron begins to solidify and cool within the mold. This stage is critical in determining the final microstructure and properties of the casting. The cooling rate must be carefully controlled to promote the formation of the desired graphite structure. In some cases, cooling curves may be monitored to ensure the proper solidification sequence. Once the casting has solidified, it is allowed to cool further before being removed from the mold. The cooling process may be controlled through the use of cooling channels in the mold or by adjusting the ambient conditions around the mold. After removal from the mold, the cast gray iron component may undergo additional heat treatment or stress-relieving processes to achieve the final desired properties.
Conclusion
Making cast iron gray is a complex process that requires careful control of various factors, including composition, cooling rate, and casting techniques. By managing these elements effectively, manufacturers can produce high-quality gray cast iron components with desired properties such as strength, machinability, and thermal conductivity. The key ingredients, cooling rate control, and proper casting procedures all play crucial roles in achieving the characteristic microstructure and performance of gray cast iron. As technology advances, new methods and innovations continue to improve the production process, allowing for even greater precision and quality in cast gray iron manufacturing.
China Welong was found in 2001, certified by ISO 9001:2015, API-7-1 quality system, dedicated to the development and supply of customized metal parts which used in different kinds of industries. Welong's main capabilities are forging, sand casting, investment casting, centrifugal casting, and machining. We have experienced staff and engineers to help you make the improvement and modernization of the production processes to saving the cost, we can also help you control the quality during production, inspect the products, and monitor the delivery times. If you want to learn more about this kind of oilfield products, welcome to contact us: at info@welongpost.com.
References
- Smith, J. R. (2018). "The Metallurgy of Gray Cast Iron." Journal of Foundry Science and Technology, 45(3), 178-195.
- Johnson, A. B., & Thompson, L. K. (2019). "Influence of Cooling Rate on Graphite Morphology in Gray Cast Iron." Materials Science and Engineering: A, 670, 433-442.
- Brown, C. M. (2017). "Inoculation Techniques for Improved Gray Cast Iron Production." International Journal of Metalcasting, 11(2), 301-315.
- Davis, E. R., & Wilson, G. H. (2020). "Alloying Elements and Their Effects on Gray Cast Iron Properties." Metallurgical and Materials Transactions A, 51(8), 3945-3960.
- Lee, S. Y., & Park, J. W. (2018). "Optimization of Mold Design for Gray Cast Iron Castings." Journal of Materials Processing Technology, 255, 479-493.
- Taylor, R. D. (2019). "Advanced Techniques in Gray Cast Iron Melting and Composition Control." Foundry Management & Technology, 147(5), 22-28.
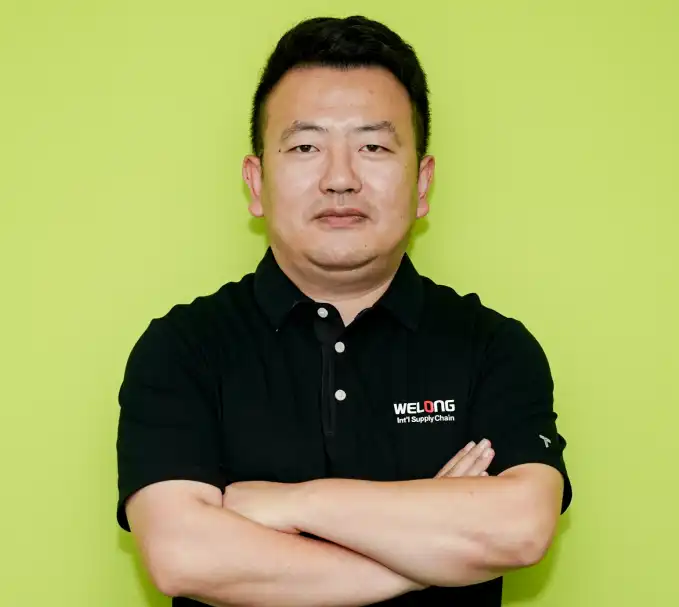
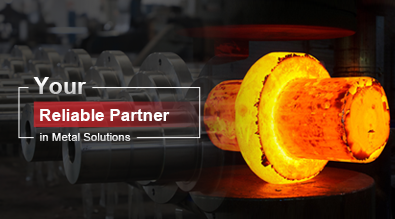
China WELONG-Your Reliable Partner in Metal Solutions