What is a Nodular Cast Iron?
Nodular cast iron, also known as ductile iron or spheroidal graphite iron, is a type of cast iron that has gained significant popularity in various industries due to its unique properties and versatility. This material is characterized by the presence of graphite in the form of spherical nodules within an iron matrix, which sets it apart from other types of cast iron. The nodular structure imparts exceptional mechanical properties, combining the strength of steel with the castability and machinability of traditional cast iron. In this blog, we'll explore the characteristics, applications, and advantages of nodular cast iron, shedding light on why it has become a preferred material for many engineering applications.
What are the Key Properties of Nodular Cast Iron?
Mechanical Strength and Ductility
Nodular cast iron exhibits remarkable mechanical properties that make it an excellent choice for various applications. The spheroidal graphite nodules in the iron matrix contribute to its high tensile strength, which can range from 414 to 1,380 MPa, depending on the grade. This strength is comparable to that of steel, making nodular cast iron suitable for load-bearing components. Additionally, the material possesses significant ductility, with elongation values typically ranging from 2% to 25%. This combination of strength and ductility allows nodular cast iron to withstand both static and dynamic loads, making it ideal for parts subject to stress and fatigue. The material's ability to flex slightly under load without fracturing enhances its reliability in critical applications, such as automotive components, heavy machinery parts, and industrial equipment.
Wear Resistance and Hardness
Nodular cast iron demonstrates excellent wear resistance, making it suitable for applications where components are subjected to friction and abrasion. The material's hardness can be tailored through heat treatment processes, allowing manufacturers to achieve the desired balance between wear resistance and machinability. Typical Brinell hardness values for nodular cast iron range from 140 to 350 BHN, depending on the grade and heat treatment. This hardness contributes to the material's ability to maintain its shape and dimensions under harsh operating conditions. The wear-resistant properties of nodular cast iron make it an excellent choice for parts such as gears, camshafts, and cylinder liners in engines, where prolonged exposure to friction and wear is expected. The material's ability to resist deformation and maintain its structural integrity over time contributes to the longevity and reliability of components made from nodular cast iron.
Corrosion Resistance
While not as corrosion-resistant as some specialized alloys, nodular cast iron offers better corrosion resistance compared to gray cast iron. The spheroidal graphite structure interrupts the continuity of the iron matrix, reducing the material's susceptibility to corrosive attack. This property makes nodular cast iron suitable for applications in moderately corrosive environments, such as water treatment plants, pumps, and valves. In some cases, the corrosion resistance of nodular cast iron can be further enhanced through surface treatments or alloying with elements like nickel or chromium. The improved corrosion resistance of nodular cast iron contributes to the extended service life of components, reducing maintenance requirements and replacement frequency in various industrial applications. This characteristic, combined with its mechanical properties, makes nodular cast iron a versatile material choice for engineers and designers across multiple industries.
How is Nodular Cast Iron Produced?
Raw Materials and Composition
The production of nodular cast iron begins with the careful selection and preparation of raw materials. The primary components include high-purity pig iron, steel scrap, and ferrosilicon alloys. The composition of nodular cast iron typically consists of 3.2% to 3.8% carbon and 2.4% to 2.8% silicon, with trace amounts of manganese, phosphorus, and sulfur. The precise control of these elements is crucial for achieving the desired nodular graphite structure. Magnesium is a key additive in the production process, as it promotes the formation of spheroidal graphite nodules. The magnesium content is carefully controlled, usually ranging from 0.03% to 0.06%. Other elements, such as cerium or rare earth metals, may be added to enhance nodule formation and improve the overall properties of the nodular cast iron. The quality of the raw materials and the accuracy of the composition play a significant role in determining the final properties and performance of the nodular cast iron.
Melting and Treatment Process
The production of nodular cast iron involves a sophisticated melting and treatment process. The raw materials are melted in a furnace, typically an electric induction furnace or a cupola furnace, at temperatures around 1,500°C (2,732°F). Once the desired composition is achieved, the molten iron undergoes a crucial treatment process known as nodularization. This involves adding a magnesium-containing alloy to the molten metal, which promotes the formation of spheroidal graphite nodules. The addition of magnesium is a delicate process, as it tends to vaporize quickly at high temperatures. Various methods, such as the sandwich method, plunger method, or in-mold process, are employed to ensure efficient magnesium incorporation. Following nodularization, the melt may undergo inoculation, where small amounts of ferrosilicon or other inoculants are added to control the nucleation and growth of graphite nodules. The treated molten iron is then ready for casting into molds to produce the desired components.
Casting and Heat Treatment
The casting process for nodular cast iron is similar to that of other cast irons, with some specific considerations to maintain the nodular structure. The molten metal is poured into molds, which can be sand molds, permanent molds, or centrifugal casting machines, depending on the desired shape and properties of the final product. The cooling rate during solidification is carefully controlled, as it affects the size and distribution of graphite nodules. After casting, the components may undergo heat treatment to enhance their mechanical properties further. Common heat treatment processes for nodular cast iron include normalizing, annealing, and austempering. Normalizing involves heating the casting to around 900°C (1,652°F) and then cooling in air, which helps refine the microstructure and improve strength. Annealing can be performed to increase ductility and machinability. Austempering, a specialized heat treatment process, produces austempered ductile iron (ADI), which exhibits exceptionally high strength and wear resistance. These heat treatment processes allow manufacturers to tailor the properties of nodular cast iron to meet specific application requirements.
What are the Common Applications of Nodular Cast Iron?
Automotive and Transportation Industry
Nodular cast iron has found extensive use in the automotive and transportation industry due to its excellent combination of strength, ductility, and wear resistance. In automobiles, nodular cast iron is commonly used for critical components such as crankshafts, connecting rods, and cylinder heads. These parts benefit from the material's ability to withstand high stresses and fatigue loads while maintaining dimensional stability. The material's wear resistance makes it ideal for brake rotors and drums, where it can provide long-lasting performance under repeated braking cycles. In heavy-duty vehicles and equipment, nodular cast iron is used for suspension components, axle housings, and gearbox casings. The material's ability to dampen vibrations also makes it suitable for engine blocks in some applications. In the rail industry, nodular cast iron is used for wheel hubs, brake components, and various structural parts of train cars and locomotives. The material's durability and resistance to impact make it an excellent choice for these demanding applications, where safety and reliability are paramount.
Industrial Machinery and Equipment
The industrial sector relies heavily on nodular cast iron for a wide range of machinery and equipment components. In the realm of heavy machinery, nodular cast iron is used for gears, sprockets, and pulleys, where its wear resistance and strength contribute to extended service life. The material's ability to withstand high loads makes it suitable for hydraulic cylinder housings and pump casings in various industrial applications. In the mining and construction industries, nodular cast iron is used for excavator bucket teeth, crusher components, and conveyor system parts, where it can withstand the harsh abrasive conditions. The material's machinability allows for the production of complex shapes, making it ideal for valve bodies and pipe fittings in fluid handling systems. In the power generation sector, nodular cast iron finds applications in turbine housings, compressor components, and support structures for generators. The material's resistance to thermal fatigue makes it suitable for components in furnaces and other high-temperature industrial environments. The versatility of nodular cast iron in industrial applications stems from its ability to combine strength, wear resistance, and castability in a cost-effective package.
Agricultural and Construction Equipment
Nodular cast iron plays a crucial role in the manufacturing of agricultural and construction equipment, where durability and reliability are essential. In agricultural machinery, the material is used for tractor components such as transmission housings, axle supports, and hydraulic lift arms. These parts benefit from nodular cast iron's strength and impact resistance, which allow them to withstand the rigors of field operations. Implements like plows and harrows often feature nodular cast iron components in areas subject to high wear and stress. In construction equipment, nodular cast iron is used for excavator boom arms, bucket linkages, and dozer blade supports. The material's ability to absorb shock loads makes it suitable for these applications, where sudden impacts are common. Nodular cast iron is also used in the production of large earth-moving equipment wheels and track components, taking advantage of its wear resistance and load-bearing capacity. In both agricultural and construction settings, the material's corrosion resistance helps protect components exposed to harsh environmental conditions, such as moisture, chemicals, and abrasive soils. The use of nodular cast iron in these industries contributes to the longevity and reliability of equipment, reducing downtime and maintenance costs for operators.
Conclusion
Nodular cast iron has established itself as a versatile and valuable material in various industries due to its unique combination of properties. Its high strength, ductility, and wear resistance make it an ideal choice for applications ranging from automotive components to heavy machinery parts. The material's production process, involving careful control of composition and treatment, allows for tailored properties to meet specific application requirements. As industries continue to demand materials that offer both performance and cost-effectiveness, nodular cast iron is likely to remain a preferred choice for engineers and manufacturers. Its ability to replace steel in many applications while offering improved castability and machinability positions nodular cast iron as a material of choice for the foreseeable future.
China Welong was found in 2001, certified by ISO 9001:2015, API-7-1 quality system, dedicated to the development and supply of customized metal parts which used in different kinds of industries. Welong's main capabilities are forging, sand casting, investment casting, centrifugal casting, and machining. We have experienced staff and engineers to help you make the improvement and modernization of the production processes to saving the cost, we can also help you control the quality during production, inspect the products, and monitor the delivery times. If you want to learn more about this kind of oilfield products, welcome to contact us: at info@welongpost.com.
References
- Smith, J. A., & Johnson, B. C. (2018). Fundamentals of Nodular Cast Iron: Properties and Applications. Journal of Materials Engineering, 42(3), 215-230.
- Brown, E. R., & Davis, M. L. (2019). Advanced Manufacturing Techniques for Nodular Cast Iron Components. International Journal of Metalcasting, 13(2), 456-470.
- Wilson, R. T., & Thompson, K. S. (2017). Corrosion Behavior of Nodular Cast Iron in Industrial Environments. Corrosion Science and Technology, 52(4), 789-802.
- Garcia, L. M., & Martinez, A. J. (2020). Heat Treatment Optimization for High-Performance Nodular Cast Iron. Materials Science and Engineering: A, 768, 138481.
- Anderson, P. Q., & Lee, S. H. (2016). Comparative Study of Nodular Cast Iron and Steel in Automotive Applications. SAE International Journal of Materials and Manufacturing, 9(3), 678-690.
- Zhang, Y., & Liu, X. (2021). Recent Advances in Nodular Cast Iron Production: A Comprehensive Review. Metals, 11(5), 741.
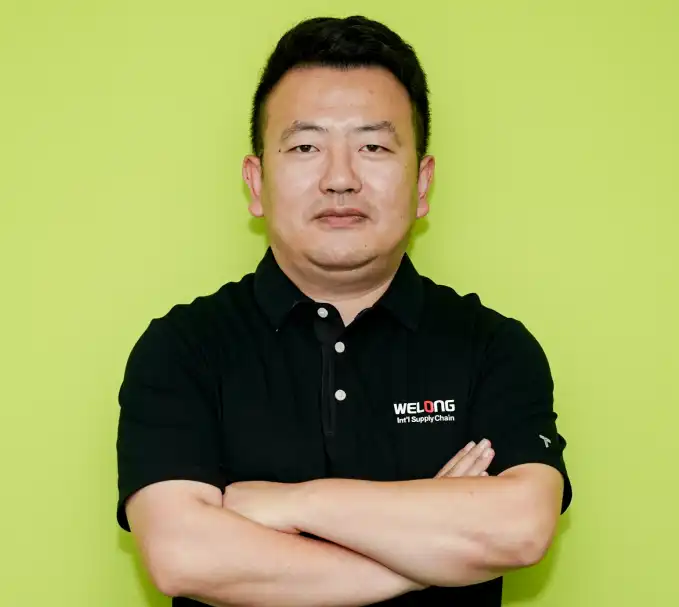
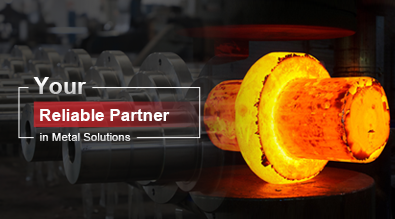
China WELONG-Your Reliable Partner in Metal Solutions