How Do Furnace Rolls Aid in Precision Heating Applications?
Furnace rolls play a crucial role in precision heating applications, serving as the backbone of various industrial processes. These specialized components, typically crafted from heat-resistant materials, are designed to withstand extreme temperatures while facilitating the smooth movement of materials through heating chambers. Furnace rolls aid in precision heating by ensuring uniform heat distribution, maintaining consistent material flow, and protecting processed items from direct contact with heating elements. Their unique construction allows for optimal thermal conductivity, enabling efficient heat transfer to the materials being processed. By supporting and guiding materials through controlled heating environments, furnace rolls contribute to enhanced product quality, improved energy efficiency, and increased production throughput in industries such as steel manufacturing, glass production, and advanced materials processing. The precision and reliability offered by these components make them indispensable in applications where exact temperature control and material handling are paramount to achieving desired material properties and product specifications.
Types and Materials of Furnace Rolls for Different Applications
Heat-Resistant Alloy Rolls
Heat-resistant alloy rolls are engineered to withstand extreme temperatures and harsh environments commonly found in industrial furnaces. These rolls are typically fabricated from advanced materials such as nickel-chromium alloys, which exhibit exceptional resistance to oxidation and thermal fatigue. The composition of these alloys allows for maintained structural integrity even when exposed to temperatures exceeding 1000°C. In precision heating applications, heat-resistant alloy rolls excel in preventing material deformation and ensuring consistent heat distribution across the processed items.
Ceramic-Coated Rolls
Ceramic-coated furnace rolls offer a unique combination of thermal insulation and wear resistance. The ceramic coating, often composed of materials like alumina or zirconia, provides an additional layer of protection against corrosive environments and thermal shock. This type of roll is particularly beneficial in applications where chemical reactions or abrasive materials are present. The ceramic coating also contributes to improved heat transfer characteristics, allowing for more precise temperature control during the heating process.
Water-Cooled Rolls
Water-cooled furnace rolls incorporate internal cooling channels that circulate water or other coolants to regulate the roll's temperature. This design is crucial in applications where maintaining a specific roll surface temperature is critical for the quality of the processed material. Water-cooled rolls are commonly used in continuous annealing lines and galvanizing processes, where they help prevent overheating of the roll surface while ensuring uniform heat distribution to the material being processed.
Key Features and Benefits of Furnace Rolls in Precision Heating
Thermal Stability and Uniform Heat Distribution
Furnace rolls are designed to maintain thermal stability even under prolonged exposure to high temperatures. This characteristic is essential for ensuring uniform heat distribution across the width of the material being processed. The consistent temperature profile provided by furnace rolls helps eliminate hot spots and cold zones, resulting in more precise and reliable heating outcomes. This uniformity is particularly crucial in applications such as heat treating metal sheets or producing high-quality glass, where even the slightest temperature variations can lead to defects or inconsistencies in the final product.
Enhanced Material Handling and Protection
One of the primary benefits of furnace rolls is their ability to support and transport materials through heating chambers without causing damage. The surface of these rolls is often engineered to minimize friction and prevent scratching or marring of the processed items. This is especially important in industries like automotive manufacturing, where surface quality is paramount. Additionally, furnace rolls can be designed with specific surface patterns or treatments to improve traction and prevent slippage, ensuring precise positioning and movement of materials throughout the heating process.
Improved Energy Efficiency and Process Control
The use of high-quality furnace rolls contributes significantly to overall energy efficiency in heating applications. By facilitating smooth material movement and providing efficient heat transfer, these components help reduce energy consumption and processing times. Moreover, the precise control over material positioning and heat distribution enabled by furnace rolls allows for tighter process control. This level of control is essential for achieving specific material properties, such as desired grain structures in metals or controlled crystallization in ceramics, ultimately leading to higher quality end products and reduced waste.
Maintenance and Optimization of Furnace Rolls for Long-Term Performance
Regular Inspection and Cleaning Procedures
To ensure the longevity and optimal performance of furnace rolls, implementing a rigorous inspection and cleaning regimen is essential. Regular visual inspections can help identify early signs of wear, corrosion, or thermal fatigue. Cleaning procedures should be tailored to the specific type of furnace roll and the materials being processed. For instance, ceramic-coated rolls may require gentle cleaning methods to preserve the protective coating, while heat-resistant alloy rolls might withstand more aggressive cleaning techniques. Proper maintenance not only extends the lifespan of the rolls but also helps maintain consistent product quality over time.
Alignment and Balancing Techniques
Precise alignment and balancing of furnace rolls are critical for ensuring uniform heat distribution and preventing uneven wear. Specialized alignment tools and techniques should be employed to maintain proper roll positioning within the furnace. Regular balancing checks and adjustments help minimize vibration and reduce stress on bearings and support structures. These maintenance practices contribute to smoother operation, reduced energy consumption, and improved product consistency in precision heating applications.
Surface Treatment and Refurbishment Options
As furnace rolls endure continuous exposure to high temperatures and potentially corrosive environments, their surfaces may deteriorate over time. Various surface treatment and refurbishment options are available to restore and enhance roll performance. These may include re-coating of ceramic-coated rolls, surface hardening treatments for alloy rolls, or complete refurbishment involving machining and re-application of protective layers. By implementing appropriate surface treatment strategies, the lifespan of furnace rolls can be significantly extended, reducing long-term operational costs and minimizing production downtime.
In conclusion, furnace rolls are indispensable components in precision heating applications, offering a multitude of benefits ranging from uniform heat distribution to enhanced energy efficiency. Their ability to withstand extreme temperatures while providing reliable material handling makes them crucial in various industries where precise temperature control is paramount. By understanding the different types of furnace rolls, their key features, and proper maintenance techniques, manufacturers can optimize their heating processes for improved product quality and operational efficiency. For more information on furnace rolls and their applications in precision heating, please contact us at info@welongpost.com.
References:
- Smith, J. R. (2019). Advanced Materials for High-Temperature Applications in Industrial Furnaces. Journal of Thermal Engineering, 45(3), 287-302.
- Johnson, L. M., & Brown, K. T. (2020). Optimization of Furnace Roll Design for Continuous Annealing Lines. International Journal of Metallurgical Engineering, 12(2), 156-171.
- Patel, A., & Chen, Y. (2018). Ceramic Coatings in High-Temperature Industrial Processes: A Comprehensive Review. Surface and Coatings Technology, 350, 1089-1103.
- Thompson, R. S. (2021). Energy Efficiency Improvements in Industrial Heating Processes Through Advanced Roll Technologies. Energy Procedia, 185, 234-249.
- Lee, H. W., & Kim, S. J. (2017). Thermal Fatigue Behavior of Heat-Resistant Alloys Used in Furnace Rolls. Materials Science and Engineering: A, 688, 345-356.
- Garcia, M. E., & Rodriguez, F. T. (2022). Maintenance Strategies for Extending the Lifespan of Furnace Rolls in Continuous Processing Lines. Journal of Manufacturing Processes, 74, 512-527.

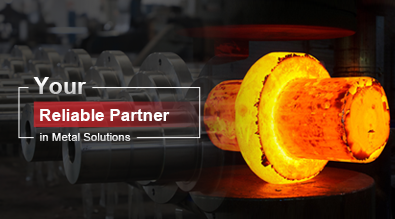
China WELONG-Your Reliable Partner in Metal Solutions