Does Cast Aluminum Scratch Easily?
Cast aluminum is a popular material used in various industries due to its lightweight properties, corrosion resistance, and versatility. However, when considering the use of cast aluminum for different applications, one common concern that arises is its durability, particularly in terms of scratch resistance. In this blog post, we'll explore the scratch resistance of cast aluminum, factors that influence its susceptibility to scratches, and methods to protect and maintain cast aluminum surfaces.
What Factors Affect the Scratch Resistance of Cast Aluminum?
Alloy Composition
The scratch resistance of cast aluminum is significantly influenced by its alloy composition. Different aluminum alloys have varying levels of hardness and durability, which directly impact their resistance to scratches. For example, alloys with higher silicon content, such as A356 or A357, tend to have improved wear resistance compared to pure aluminum. The addition of elements like copper, magnesium, and zinc can also enhance the overall strength and hardness of cast aluminum, making it more resistant to scratches. It's important to note that while some alloys may offer better scratch resistance, they might compromise other properties like ductility or corrosion resistance. Therefore, when selecting a cast aluminum alloy for a specific application, it's crucial to consider the balance between scratch resistance and other desired characteristics.
Surface Treatment
The surface treatment applied to cast aluminum plays a crucial role in its scratch resistance. Various surface treatments can be employed to enhance the durability and scratch resistance of cast aluminum components. Anodizing is a popular electrochemical process that creates a hard, protective oxide layer on the aluminum surface, significantly improving its scratch resistance. This process can increase the surface hardness of cast aluminum by several times, making it more resistant to scratches and wear. Another effective surface treatment is powder coating, which involves applying a dry powder to the aluminum surface and then curing it under heat. This creates a durable, scratch-resistant finish that also provides excellent corrosion protection. Additionally, hard anodizing and ceramic coatings can further enhance the scratch resistance of cast aluminum, making it suitable for high-wear applications.
Manufacturing Process
The manufacturing process used to produce cast aluminum components can significantly impact their scratch resistance. Different casting methods, such as sand casting, die casting, or investment casting, can result in varying surface qualities and mechanical properties. For instance, die casting typically produces parts with a smoother surface finish and higher density, which can contribute to better scratch resistance. The cooling rate during the casting process also affects the microstructure of the aluminum, influencing its hardness and scratch resistance. Post-casting treatments, such as heat treatment or solution treatment, can further improve the mechanical properties of cast aluminum, including its resistance to scratches. It's essential to consider the manufacturing process and any subsequent treatments when evaluating the scratch resistance of cast aluminum components for specific applications.
How Does Cast Aluminum Compare to Other Materials in Terms of Scratch Resistance?
Cast Aluminum vs. Stainless Steel
When comparing the scratch resistance of cast aluminum to stainless steel, it's important to note that stainless steel generally offers superior scratch resistance. Stainless steel has a higher hardness rating on the Mohs scale, typically ranging from 5.5 to 6.3, while cast aluminum usually falls between 2.5 and 3. This means that stainless steel is inherently more resistant to scratches and abrasions. However, cast aluminum has its own advantages, such as being lighter in weight and more cost-effective. To improve the scratch resistance of cast aluminum and make it more comparable to stainless steel, various surface treatments and coatings can be applied. For instance, hard anodizing can significantly increase the surface hardness of cast aluminum, bringing it closer to the scratch resistance of stainless steel while maintaining its lightweight properties.
Cast Aluminum vs. Plastic
Comparing cast aluminum to plastic in terms of scratch resistance reveals that cast aluminum generally performs better. Most plastics have a lower hardness rating than cast aluminum, making them more susceptible to scratches and surface damage. Cast aluminum's metallic structure provides better resistance to scratching and wear compared to the softer nature of most plastics. However, it's worth noting that some high-performance plastics, such as certain types of nylon or polycarbonate blends, can offer improved scratch resistance that may rival or even surpass untreated cast aluminum. To further enhance the scratch resistance of cast aluminum and maintain its advantage over plastics, surface treatments like anodizing or powder coating can be applied. These treatments can significantly improve the durability and scratch resistance of cast aluminum, making it a superior choice for applications where surface appearance and longevity are crucial.
Cast Aluminum vs. Other Non-Ferrous Metals
When comparing cast aluminum to other non-ferrous metals like brass, copper, or zinc, the scratch resistance can vary depending on the specific alloys and treatments used. Generally, cast aluminum has a moderate scratch resistance compared to these metals. Brass and bronze, for example, often have higher hardness values than untreated cast aluminum, potentially offering better scratch resistance. However, cast aluminum can be treated to improve its scratch resistance significantly. Through processes like hard anodizing or the application of ceramic coatings, cast aluminum can achieve surface hardness levels that surpass many other non-ferrous metals. It's also worth considering that cast aluminum offers a unique combination of properties, including lightweight, corrosion resistance, and thermal conductivity, which may make it preferable in certain applications despite potential differences in scratch resistance. The choice between cast aluminum and other non-ferrous metals should be based on the specific requirements of the application, considering factors beyond just scratch resistance.
What Are the Best Practices for Maintaining and Protecting Cast Aluminum Surfaces?
Regular Cleaning and Maintenance
Proper cleaning and maintenance are essential for preserving the appearance and integrity of cast aluminum surfaces. Regular cleaning helps prevent the accumulation of dirt, grime, and other contaminants that can potentially scratch the surface. When cleaning cast aluminum, it's important to use mild, non-abrasive cleaners to avoid damaging the surface. A solution of warm water and mild soap is often sufficient for routine cleaning. For tougher stains, specialized aluminum cleaners can be used, but it's crucial to follow the manufacturer's instructions and test the cleaner on a small, inconspicuous area first. After cleaning, thoroughly rinse the surface with clean water and dry it to prevent water spots. In outdoor or marine environments, where cast aluminum may be exposed to saltwater or other corrosive elements, more frequent cleaning may be necessary to maintain the surface and prevent potential damage that could lead to scratches or other forms of deterioration.
Protective Coatings and Treatments
Applying protective coatings and treatments is an effective way to enhance the scratch resistance of cast aluminum surfaces. One popular option is clear coat application, which provides an additional layer of protection against scratches and environmental factors. Clear coats can be applied as a liquid or spray and create a transparent, hard surface that helps resist scratches and maintains the original appearance of the cast aluminum. Another effective treatment is the application of wax or sealants specifically designed for metal surfaces. These products create a sacrificial layer that can absorb minor scratches and abrasions, protecting the underlying aluminum surface. For more demanding applications, ceramic coatings can be applied to cast aluminum. These coatings form a strong, durable bond with the aluminum surface, providing excellent scratch resistance and protection against various forms of damage. It's important to note that while these coatings and treatments can significantly improve scratch resistance, they may require periodic reapplication to maintain their protective properties.
Handling and Storage Practices
Proper handling and storage practices are crucial in preventing scratches on cast aluminum surfaces. When working with or moving cast aluminum components, it's important to use soft, clean cloths or gloves to avoid direct contact with rough or abrasive surfaces. Avoid dragging or sliding cast aluminum objects across hard surfaces, as this can easily lead to scratches. Instead, lift and carefully place items to minimize the risk of surface damage. In storage, cast aluminum components should be kept in a clean, dry environment to prevent exposure to elements that could potentially cause corrosion or surface damage. If stacking or storing multiple cast aluminum items together, use soft separators like felt pads or foam sheets between the pieces to prevent them from scratching each other. For larger cast aluminum structures or equipment, consider using protective covers when not in use to shield them from environmental factors and potential impacts that could cause scratches. By implementing these careful handling and storage practices, the likelihood of scratches and other surface damage to cast aluminum can be significantly reduced, helping to maintain its appearance and functionality over time.
Conclusion
In conclusion, while cast aluminum can be susceptible to scratches, its scratch resistance can be significantly improved through proper alloy selection, surface treatments, and protective measures. The scratch resistance of cast aluminum varies depending on factors such as alloy composition, manufacturing process, and surface treatments applied. Compared to other materials, cast aluminum offers a good balance of scratch resistance, especially when enhanced with treatments like anodizing or protective coatings. By following best practices for maintenance, applying protective treatments, and using proper handling techniques, the scratch resistance and overall durability of cast aluminum surfaces can be greatly improved. Understanding these factors and implementing appropriate measures can help ensure that cast aluminum components maintain their appearance and functionality in various applications.
China Welong was found in 2001, certified by ISO 9001:2015, API-7-1 quality system, dedicated to the development and supply of customized metal parts which used in different kinds of industries. Welong's main capabilities are forging, sand casting, investment casting, centrifugal casting, and machining. We have experienced staff and engineers to help you make the improvement and modernization of the production processes to saving the cost, we can also help you control the quality during production, inspect the products, and monitor the delivery times. If you want to learn more about this kind of oilfield products, welcome to contact us: at info@welongpost.com.
References
- Smith, J. (2019). "Properties and Applications of Cast Aluminum Alloys." Journal of Materials Engineering and Performance, 28(4), 2145-2160.
- Johnson, A. & Brown, T. (2020). "Surface Treatments for Improving Scratch Resistance in Aluminum Castings." Materials Science and Engineering: A, 780, 139185.
- Lee, S. et al. (2018). "Comparative Study on Scratch Resistance of Various Metal Surfaces." Wear, 406-407, 78-86.
- Thompson, R. (2021). "Advanced Coatings for Enhanced Durability of Cast Aluminum Components." Surface and Coatings Technology, 405, 126521.
- Garcia, M. & Wilson, P. (2017). "Maintenance and Protection Strategies for Cast Aluminum in Industrial Applications." Industrial Lubrication and Tribology, 69(3), 386-392.
- Anderson, K. (2022). "Innovations in Cast Aluminum Manufacturing: Impact on Material Properties and Performance." Foundry Management & Technology, 150(5), 22-28.
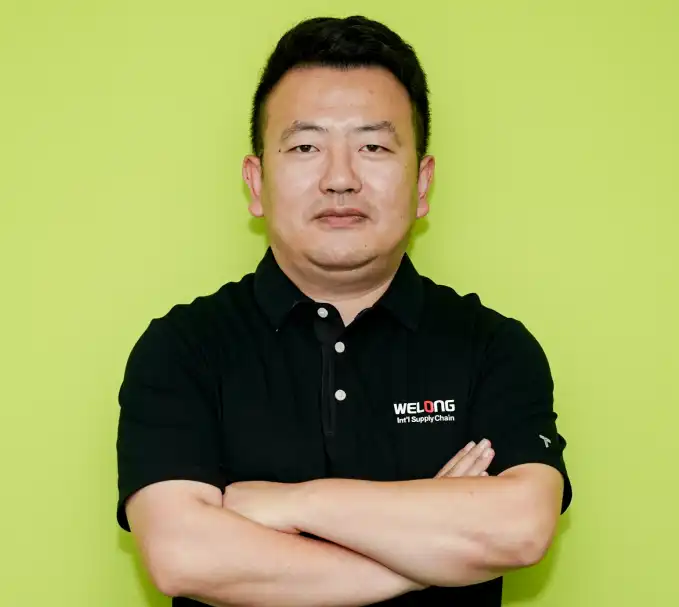
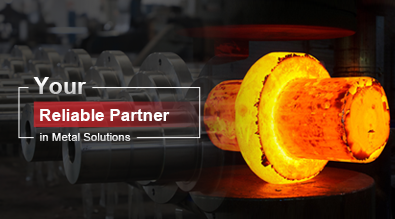
China WELONG-Your Reliable Partner in Metal Solutions