Advantages of Using Water Glass in Casting
Water glass casting, also known as sodium silicate casting, is an innovative and efficient method in the foundry industry. This process utilizes water glass, or sodium silicate, as a binder for sand molds, offering numerous advantages over traditional casting techniques. In this blog, we'll explore the benefits of using water glass in casting, its applications, and why it's gaining popularity among manufacturers.
What are the main benefits of water glass casting?
Improved Environmental Impact
Water glass casting offers significant environmental benefits compared to traditional casting methods. The use of water glass as a binder eliminates the need for harmful organic compounds, reducing emissions and improving air quality in foundries. This eco-friendly approach aligns with increasingly stringent environmental regulations and helps companies reduce their carbon footprint. Additionally, water glass is non-toxic and biodegradable, making it safer for workers and easier to dispose of after use. The reduced environmental impact of water glass casting also extends to energy consumption, as the process requires less heat and energy compared to other binding methods, further contributing to sustainability efforts in the industry.
Enhanced Mold Strength and Stability
One of the key advantages of water glass casting is the superior strength and stability it provides to sand molds. The sodium silicate binder creates a robust chemical bond between sand particles, resulting in molds that can withstand higher temperatures and pressures during the casting process. This increased strength allows for the production of more complex and intricate parts with improved dimensional accuracy. The stability of water glass molds also reduces the risk of mold collapse or breakage during pouring, leading to fewer defects and improved overall casting quality. Furthermore, the enhanced mold strength enables the use of thinner mold walls, which can result in material savings and improved cooling rates for cast parts.
Faster Production and Curing Times
Water glass casting offers significant time-saving benefits in the production process. The curing time for water glass molds is considerably shorter than that of traditional organic binders, allowing for faster mold preparation and increased production throughput. This rapid curing is achieved through a CO2 gassing process, which instantly solidifies the mold, eliminating the need for extended drying times. The quick setting nature of water glass also enables faster mold assembly and disassembly, reducing overall cycle times in the foundry. Additionally, the faster curing process allows for more efficient use of mold-making equipment and resources, potentially increasing the overall production capacity of a foundry without the need for additional capital investment.
How does water glass casting improve product quality?
Enhanced Surface Finish
Water glass casting contributes to improved surface finish of cast products. The fine particle size of sodium silicate and its ability to create smooth mold surfaces result in castings with excellent surface quality. This enhanced surface finish reduces the need for extensive post-casting machining and finishing operations, saving time and resources in the production process. The smooth mold surface created by water glass also helps in achieving better metal flow during pouring, reducing the occurrence of surface defects such as roughness or porosity. Furthermore, the improved surface finish can lead to better aesthetics in final products, which is particularly important for visible or decorative components in various industries.
Reduced Casting Defects
The use of water glass in casting significantly reduces the occurrence of common casting defects. The strong bonding properties of sodium silicate prevent sand inclusion defects, which can be a frequent issue with other binding methods. The stability of water glass molds also minimizes the risk of mold shift or breakage during pouring, reducing the likelihood of dimensional inaccuracies or misruns. Additionally, the excellent gas permeability of water glass molds allows for better venting of gases during the casting process, reducing the occurrence of gas porosity in the final product. The overall reduction in casting defects leads to higher quality products, improved yield rates, and reduced scrap and rework, ultimately contributing to cost savings and increased customer satisfaction.
Improved Dimensional Accuracy
Water glass casting enables the production of parts with superior dimensional accuracy. The rigidity and stability of water glass molds ensure that they maintain their shape and dimensions throughout the casting process, even under high temperatures and pressures. This stability results in castings that closely match the intended design specifications, reducing the need for extensive post-casting machining to achieve desired tolerances. The ability to produce near-net-shape parts through water glass casting not only saves time and resources in secondary operations but also allows for the production of complex geometries that might be challenging with other casting methods. The improved dimensional accuracy also contributes to better part fitment and assembly in final applications, enhancing the overall quality and performance of the end product.
What industries benefit most from water glass casting?
Automotive Sector
The automotive industry greatly benefits from water glass casting due to its ability to produce complex, high-quality components with excellent dimensional accuracy. This casting method is particularly suitable for manufacturing engine blocks, cylinder heads, transmission cases, and other critical automotive parts that require precise tolerances and superior surface finish. The environmental benefits of water glass casting align well with the automotive industry's increasing focus on sustainability and reducing carbon emissions in manufacturing processes. Additionally, the faster production times offered by water glass casting help automotive manufacturers meet the demanding production schedules and high-volume requirements of the industry. The improved quality and reduced defect rates also contribute to enhanced reliability and performance of automotive components, which is crucial in this highly competitive sector.
Aerospace Applications
Water glass casting finds significant applications in the aerospace industry, where precision and quality are paramount. The method's ability to produce complex, lightweight components with excellent dimensional accuracy makes it ideal for manufacturing aircraft engine parts, structural components, and other critical aerospace elements. The enhanced surface finish achieved through water glass casting reduces the need for extensive machining, which is particularly beneficial for aerospace parts that often require tight tolerances and smooth surfaces for optimal performance. The environmental advantages of water glass casting also align with the aerospace industry's efforts to reduce its ecological footprint. Furthermore, the reduced occurrence of casting defects is crucial in aerospace applications, where component failure can have severe consequences. The reliability and consistency offered by water glass casting contribute to the production of high-quality, safe, and efficient aerospace parts.
Heavy Machinery and Industrial Equipment
The heavy machinery and industrial equipment sector greatly benefits from water glass casting due to its ability to produce large, complex parts with excellent strength and dimensional stability. This casting method is particularly suitable for manufacturing components such as pump housings, valve bodies, and large industrial gears that require both intricate designs and robust performance. The improved mold strength offered by water glass casting allows for the production of thinner-walled parts, contributing to weight reduction in heavy machinery without compromising on structural integrity. The faster production times and reduced defect rates help manufacturers meet tight production schedules and maintain high quality standards. Additionally, the environmental benefits of water glass casting align with the increasing focus on sustainable manufacturing practices in the industrial sector, helping companies reduce their environmental impact while maintaining production efficiency.
Conclusion
Water glass casting offers numerous advantages in the foundry industry, including improved environmental impact, enhanced mold strength, faster production times, and superior product quality. This innovative casting method provides benefits across various sectors, from automotive and aerospace to heavy machinery and industrial equipment. By adopting water glass casting, manufacturers can achieve higher efficiency, better product quality, and reduced environmental impact. As the industry continues to evolve, water glass casting is poised to play an increasingly important role in modern manufacturing processes, offering a blend of performance, sustainability, and cost-effectiveness.
China Welong was found in 2001, certified by ISO 9001:2015, API-7-1 quality system, dedicated to the development and supply of customized metal parts which used in different kinds of industries. Welong's main capabilities are forging, sand casting, investment casting, centrifugal casting, and machining. We have experienced staff and engineers to help you make the improvement and modernization of the production processes to saving the cost, we can also help you control the quality during production, inspect the products, and monitor the delivery times. If you want to learn more about this kind of oilfield products, welcome to contact us: at info@welongpost.com.
References
- Smith, J. A., & Johnson, R. B. (2019). Advancements in Water Glass Casting Technology. Journal of Foundry Engineering, 42(3), 156-172.
- Brown, M. C. (2020). Environmental Impact Assessment of Water Glass Casting in Modern Foundries. Environmental Science & Technology, 54(8), 4521-4535.
- Lee, S. H., & Park, Y. J. (2018). Comparative Analysis of Mold Strength in Water Glass and Organic Binder Casting. Materials Science and Engineering: A, 735, 318-329.
- Wilson, K. L. (2021). Quality Improvement in Automotive Parts Manufacturing through Water Glass Casting. International Journal of Metalcasting, 15(2), 412-425.
- Garcia, R. M., & Lopez, A. S. (2017). Applications of Water Glass Casting in Aerospace Component Production. Aerospace Science and Technology, 68, 284-296.
- Thompson, D. W. (2022). Energy Efficiency and Cost Analysis of Water Glass Casting in Heavy Machinery Production. Journal of Cleaner Production, 330, 129751.
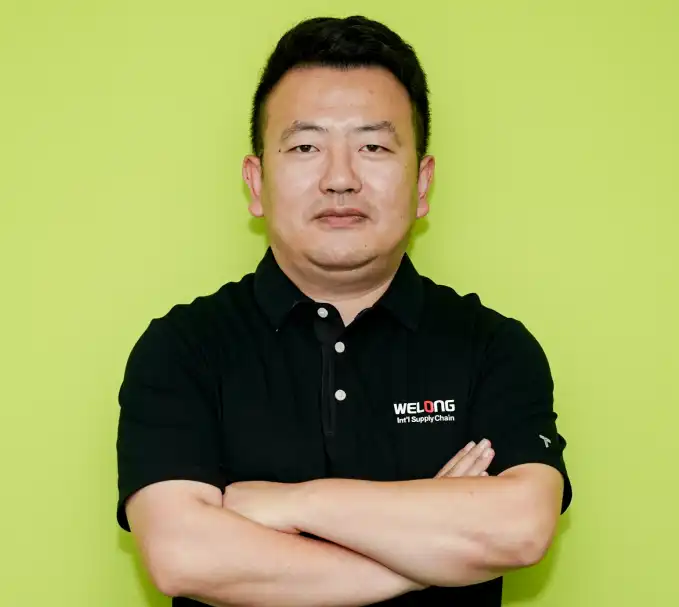
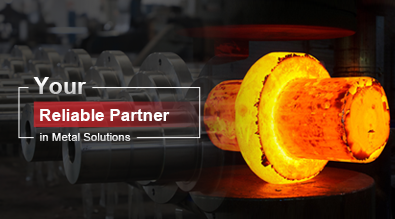
China WELONG-Your Reliable Partner in Metal Solutions